مقدمه
استفاده از ورق فولاد قلع انـدود جهـت بسـته بنـدی موادغـذایی تاریخچـه طـولانی دارد. در اوایـل قـرن نوزدهم میلادی، ناپلئون جایزه ای به مبلغ ۱۲۰۰۰ فرانک برای ارائـه روشـی کـه بـه وسـیله آن بتـوان موادغـذایی مصرفی ارتش آن کشور را نگهداری کرد تعیین و اعلام نمود.
در آن هنگام نیکلا آپرت به این نکته پی برد کـه می توان با حرارت دادن ماده غذایی و نگهداری آن دور از هوا، ماده غذایی را به مدت طولانی حفـظ نمـود. وی در این زمینه ظروف شیشه ای را بکار گرفـت، ایـن تجربـه بعـدها اسـاس صـنعت کنسروسـازی قـرار گرفـت. دو مهندس انگلیسی به نام های جان هال و برایان دانکین، شروع به تولید قوطی از ورق قلع اندود جهـت بسـته بنـدی موادغذایی دریانوردان نمودند. ورق ها در آن موقع نسبتا نـاهموار بـوده و دارای پوششـی ضـخیم از قلـع بودنـدو قلع اندود کردن نیز به روش غوطه وری انجام میگرفت.
در سال ۱۸۱۹ برای اولین بار قوطی قلع اندود به صورت تجاری وارد بازار شد. از سال ۱۸۶۰ هنر قوطی سازی کامل تر شده و به صورت علم درآمـد. در سـال ۱۹۲۹، در آلمان از روش الکترولیتی برای قلع اندود کردن استفاده شد که در این حالت مصـرف قلـع بـه نحـو چشـمگیری کاهش یافت.
نحوه تهیه ورق فولادی
پــس از آنکــه ســنگ آهــن در کارخانجــات ذوب، بــه صــورت آهــن مــذاب درآمــد، تــوده مــذاب در کارگاه های ریختهگری به شکل تختال (slab) ضخیم طویل در می اید. معمولا تختالی که برای تولید ورق مورد استفاده قرار می گیرد، از نوع کم کربن است. طول تختال بین ۹ تا ۱۰ متر، عرض آن بین ۶۵ سانتی متر تا ۲ متـر و ضخامت آن ۲۲ سانتی متر مـی باشـد. حـداکثر وزن تختـال بـه هنگـام خـروج از قالـب، ۲۸ تـن اسـت. تختـال در مرحله ای که قرار است تبدیل به ورق شود، توسط کوره های مخصوص گرم شده و سـپس طـی چنـد مرحلـه بـا عبور از نورد گرم که غلطک هایی با فاصله (clearance) معین هستند، تبدیل به ورقی به ضـخامت ۱/۸ میلـیمتـر در می آید. این ورق سپس در حمام اسید سولفوریک رقیق اسیدشویی شـده و توسـط نـورد سـرد، ضـخامت آن به۰/۵ تا ۰/۱۵ میلی متر خواهد رسید. در نهایت ورقه، استرس زدایی شده تا بـدین ترتیـب سـختی و سـطح صـاف مورد نظر بدست آید . تنش زدایی یا آنیل محفظهایی box annealing) )، شامل حـرارتدهـی و خنـک سـازی آرام کلاف ها به منظور از بین بردن تنشهای تولید شده در حین نورد سرد است. این فرآیند که در یک محفظـه آب بندی شده انجام می گیرد با وارد کردن گاز خنثی یا گازی که به طور جزیی احیا باشد، سـطحی بـراق ایجـاد مینماید. با توجه به اینکه هرچه از ضخامت ورق کاسته شود، صرفهجویی بیشتری در هزینـه هـا صـورت خواهـد گرفت و نیز با توجه به این واقعیت که هر چه ورق نـازک تـر شـود، بواسـطه فشـار وارده بـه آن، سـختی آن نیـز افزایش می یابد، بنابراین اکنـون اسـتفاده از ورق هـایی کـه دوبـار توسـط نـورد سـرد تیمـار شـده انـد و بـه DCR
(doublecold reduced) موسوم میباشند، معمول میباشد.
در صورتی که تختال ها بعد از شکل گیری به انبار تختال منتقل شده باشند، ابتـدا آنهـا را در کـوره هـایی گرم می نمایند تا مجددا به صورت گداخته درآیند و سپس با استفاده از غلطک های عمودی و افقی از ضـخامت آن ها کاسته خواهد شد. این غلطک ها قادر هستند که در حین کاهش ضخامت، عرض تختال را نیز حـداکثر تـا
۷۰ میلی متر کاهش دهند. جهت برداشتن پوسته هایی که بر روی صفحات فولادی (تختـال نـازک شـده) بوجـود می ایند از دو غلطک دیگر به نام «pinch roll» که فشار مضاعفی بر صفحه وارد میکند، به همـراه آب بـا فشـار زیاد، استفاده می گردد. نورد گرم با سیستمهای کنترل ضخامت و کنترل ابعاد مجهز است و درجـه حـرارت ورق خروجی از نورد حدود ۸۵۰ درجه سانتیگراد خواهد بود که رفته رفته تا ۶۰۰ درجه سـانتیگـراد خنـک شـده و سپس به کلاف پیچ منتقل می گردد. این کلافها آماده انتقال به واحد نورد سرد هستند. کلافها دارای عـرض بـین
۵۸ سانتی متر تا کمی کمتر از ۲ متر بوده، قطر آنها حداکثر به یک متر و ۸۵ سانتیمتر میرسـد و وزن کـلاف در این هنگام حدود ۲۷ تن است.
قلع اندود نمودن ورق
پوشاندن صفحات فولادی توسط قلع ابتدا با غوطهور نمودن صفحات در حمام مـذاب (غوطـهوری داغ)
صورت می گرفت. گرچه هنوز هم از این روش استفاده می شود، اما بخش عمده ورقهای قلـع انـدود امـروزه بـه روش الکترولیتی تولید می شوند. در روش غوطه وری، لایه ای نسبتا ضخیم از قلع ۱۷) تا ۲۲ گرم بـه ازاء هـر متـر مربع، ۸/۵ تا ۱۱ گرم بر روی هر سطح) تشکیل میگردد که معادل ضخامتی حدود ۰/۰۲ تا ۰/۰۷ میلیمتر در هـر سوی ورق خواهد بود. شرط لازم برای قلع اندود کردن به روش فوق، وجود سطحی تمیـز و عـاری از آلـودگی است که این عمل با اسیدشویی و توسط اسید سولفوریک یا کلریدریک رقیق انجام میگیرد. غلظت اسید ۲ تا ۶
درصد و دما در محدوده ۶۵-۸۰ درجه سانتی گراد و زمان اسید شویی ۲-۴ دقیقـه اسـت. ورق هـا سـپس از میـان حوضچه روان ساز به عمق ۲/۵-۵ سانتیمتر عبور مینمایند. روان ساز مورد استفاده معمولا کلرور روی Zn Cl2)
) محلول در آب است که حاوی مقداری کلرید آلومینیوم نیز می باشد. سرعت عبـور ورق از میـان محلـول روان ساز حدود ۱۶/۵ سانتی متر بر ثانیه است. پس از روان سازی، ورق وارد پاتیل قلع مذاب شده و در مرحله بعـد بـه صورت عمودی از لایه روغن و غلطکهای خشککن عبور مینمایند.
در روش الکترولیتی، مصرف قلع به ۵/۶ گرم به ازای هر متر مربع ۲/۸) گرم بر هر طرف) کاهش یافته و ضخامت آن به حدود ۰/۴ میکرومتر خواهد بود. نحوه عمل قلع اندود کردن به روش الکترولیتـی را مـیتـوان در شکل ۱ ملاحظه نمود.
شکل -۱ نمودار تولید ورق قلع اندود ورق های حاصل از نورد سرد، پس از بـاز شـدن، توسـط قلیـا، آب و اسـید شسـته مـی شـود. در مرحلـه
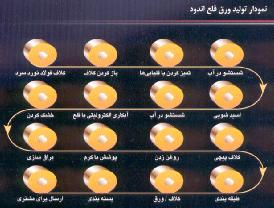
شستشوی قلیایی، گرد و خاک، ذرات فلزی و جامدات موم مانند جدا میشوند. تمیزکننده های قلیـایی مخلـوطی از نمک های معدنی همراه با مقادیر کمی خیس کننده ها هستند تا بتوانند تمیزکاری را از طریق صـابونی شـدن و تشکیل امولسیون را بهبود بخشند. در عملیات اسیدشویی جهت دفع اکسیدهای فلزی از اسید اسـتفاده مـی گـردد که اسید سولفوریک متداول ترین این اسیدها به شمار می آید. اسید پس از حل پوسته اکسیدی، بـه پایـه فـولادی حمله می کند، بنابراین از ممانعت کننده ها باید استفاده شود. پس از تمیز کردن ورق، آنها را وارد حوضـچه هـای آبکاری (الکترولیتی) می نمایند. این بخش خود از چندین سلول آب کاری (معمـولا۵-۱۲ ۲ عـدد) تشـکیل شـده است. در ابتدای بخش، سلول آب کاری اولیه قرار دارد که حاوی الکترولیتی کاملا یـا تـا انـدازه ای متفـاوت بـا حمام اصلی است. در این سلول ها شمش خالص قلع، آنـد و ورق، کاتـد را تشـکیل مـی دهـد. ورق قلـع انـدود و الکترولیتی را می توان با مقادیر برابر یا نابرابر قلـع روی دو سـطح ورق تولیـد نمـود (جـدول.(۱ ضـخامت اسـمی پوشش قلع برای نوع برابر بین ۰/۴ تا ۱/۵ میکرومتر روی هر سطح تغییر میکند و ضخامت نهایی پوشش با عبـور نوار از یک سلول به سلول بعدی بدست می آید. بعد از خروج نوار از آخرین سلول آب کاری، ورق قلع انـدود، بلافاصله شستشو شده و خشک می گردد تا از رگه دار شدن آن جلوگیری گردد. برج های ذخیره نوارکه در ابتدا و انتهای فرآیند دیده می شوند، نوارهای اضافی را ذخیره می نمایند تا در صورت بـروز مشـکل، پیوسـتگی خـط، قطع نشود (شکل .(۲ با مطالعه قوانین فاراده و با شناخت واکنش های الکترودها می توان پوشـش دهـی الکتریکـی قلع را کنترل کرد. قلع پوشانی الکترولیتی در الکترولیت های اسیدی و یا قلیایی انجام می شود. در فرآیند اسیدی، واکنش آند، اکسیداسیون مستقیم قلع فلزی به یون قلع دوظرفیتی است.
°Sn ® Sn++ + ۲e– | ||||
جدول -۱ مشخصات ورق قلع اندود | ||||
نوع پوشش | علامت فعلی | علامت قبلی | ||
یکسان | ۲/۸-۲/۸ | #۲۵ | ||
۵/۶-۵/۶ | #۵۰ | |||
۸/۴-۸/۴ | #۷۵ | |||
متفاوت | ۲/۸-۵/۶ | #۲۵-۵۰ | ||
۲/۸-۸/۴ | #۲۵-۷۵ | |||
۵/۶-۸/۴ | #۵۰-۷۵ |
در اثر این واکنش قلع فلزی روی کاتد رسوب می کند که در فرآیند مداوم، کاتد، نوار پیوسته فـولادی متحرک است (شکل .(۳ رسوب قلع در محیط اسیدی چسبندگی کمتری نسبت به رسوب قلع در محـیط قلیـایی دارد که این ضعف را میتوان با انجام روشهای نظافت سطح تا حدودی برطرف نمـود و یـا مـوادی آلـی ماننـد ژلاتین به محلول افزود. شکل -۲ بخش های اصلی تولید ورق قلع اندود
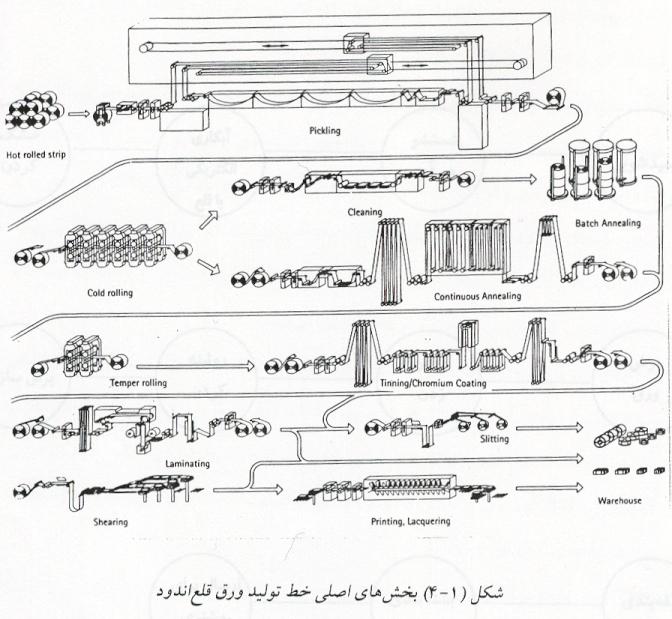
شکل -۳ نحوه تثبیت قلع بر روی ورق فولادی همچنین حضور عامل تر کننده مانند- ß نفتول ضروری است. حمـام هـای اسـیدی مناسـب بـرای فرآینـد
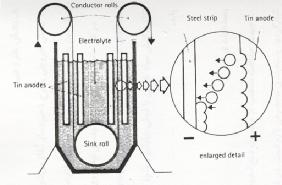
قلع اندود کردن متنوع بوده و از جمله به حمام اسید سولفونیک، حمام فلوئورید، کلریـد، سـولفات و فلوئـوبرات می توان اشاره نمود. در فرآیند الکترولیتی قلیایی، از حمام های قلیایی استات سدیم یـا پتاسـیم اسـتفاده مـی شـود.
واکنش آند، اکسیداسیون قلع فلزی به یون قلع چهار ظرفیتی است.
Sn ° ® Sn ۴+ + ۳e–
در این فرآیند در اثر انحلال یـک اتـم قلـع، چهـار الکتـرون ولـی در فرآینـد اسـیدی دو الکتـرون آزاد می شود، بنابراین انحلال یک مولکول گرم قلع در الکترولیت قلیایی، مستلزم مصرف جریـان الکتریکـی دو برابـر است.در مقایسه دو روش، روش اسیدی را روش مناسبتری میدانند زیرا حمامهای قلیایی در دمای بـیش از ۹۵
کرده استدرجه سانتی گراد بازدهی دارند در حالیکه حمام اسیدی در محدوده ۳۸-۴۹ درجه سانتی گراد عمل می نماید. در روش اسیدی هیدروژن کمتری در آند تولید می شود، مصرف جریان الکتریکی نصـف روش قلیـایی اسـت و بـه فضای ساختمانی کمتری نیاز دارد، ضمن آنکه از سرعت پوششدهی بالاتری برخوردار است. روش اسیدی البته دارای معایبی نیز میباشد که عبارتند از:
الف: انحلال قلع در آند بیشتر از رسوب قلع بر کاتد (نوار فولادی) است، در نتیجه محلـول الکترولیـت همـواره حاوی مقدار اضافی یون است و در نتیجه ضخامت لایه قلع غیر یکنواخت خواهد شد.
ب: با پیشرفت انحلال، آند تحلیل رفته، فاصله بین آند و نوار فولادی (کاتد) تغییر میکند و بنـابراین لازم اسـت آند به طرف نوار حرکت داده شود.
ج: لزوم جایگزینی مکرر آند که بازدهی فرآیند را کم میکند.
د: شکسته شدن آند درحین تعویض یا حرکت.
سفیدگری
(Flow Brightening)
ورق قلعاندود تهیه شده به روش غوطهوری دارای ظاهری درخشان و براق است، در حالیکه، قلع اندود نمودن به روش الکترولیتی، سطحی گرفته و مات ایجاد میکند. در این حالت ورق قلع اندود شده دارای مورفولوژی میکروکریستالی غیرانعکاسی است. علت بروز این حالت آن است که یونهای قلع حاصل از آند، به صورت ذرهای بر روی نوار فولادی رسوب مینمایند و بنابراین نوعی حالت متخلخل را ایجاد خواهند نمود.
برای رفع این وضعیت، نوار قلع اندود شده، به یکی از روشهای مقاومت الکتریکی، القاء و یا حمام روغن داغ،
سریعا حرارت میبیند. اگر چه نقطه ذوب قلع ۲۳۱/۹ درجه سانتیگراد است، اما برای حصول اطمینان از ذوب کامل و ظاهر یکنواخت، لازم است تا نوار را تا دمایی بالاتر از این حد گرم نمود. این فرآیند را سفیدگری مینامند که نه تنها ظاهر ورق را بهبود محسوس میبخشد و آن را به حالت براق و درخشان در می اورد بلکه مقاومت آن را به خوردگی نیز افزایش میدهد.
روئین سازی
(Passivation)
در عملیاتی دیگر، و به منظور جلوگیری از تشکیل اکسید قلع بر سطح نوار، لایهای ازکروم و اکسید کروم هیدراته بر روی نوار قلع اندود تثبیت میشود، در صورت باقیماندن اکسید قلع، نه تنها نوار به مرور زمان بد رنگ میشود، لعاب دهی به سطح داخلی ورق و لحیمکاری لبه ها دشوار خواهد شد. در این روش از محلول دی کرومات سدیم الکترولیتی با غلظت ۲۰ تا ۶۰ گرم در لیتر و pH برابر با ۳/۵ تا ۷ و دمای حمام ۳۵ تا ۷۰ درجه سانتیگراد استفاده میگردد. دانسیته جریان ۵-۴۰ A/dm2 بوده و زمان عملیات ۰/۱ تا ۱۰ ثانیه میباشد.
محدوده بهینه اکسید کروم هیدراته که بر روی ورق قلع اندود قرار میگیرد، ۰/۰۰۵ تا ۰/۰۵ گرم به ازای هر مترمربع است، در صورتی که مقدار اکسیدکروم کمتر از ۰/۰۰۵ گرم بر هر مترمربع و یا بیشتر از ۰/۰۵ گرم بر هر مترمربع باشد، مقاومت به خوردگی کاهش یافته، لعاب پذیری هم افت مینماید.
به هر روی پس از پایان عملیات روئین سازی، نوار با آب حاوی اسید سیتریک به طوریکه pH بین ۵-۶ باشد شسته میشود تا خاصیت چاپپذیری ورق بهبود یابد.گاهی نیز از کربنات سدیم استفاده میشود که اثر کمتری در مقایسه با محلول فوق دارد و بیشتر در قوطی های کنسانتره شیر از آن استفاده میگردد.
روغن کاری
بعد از انجام همه عملیات فوق، با توجه به اینکه ماشینهای قوطی ساز از سرعت بالایی برخوردار هستند، لازم است تا سطح ورق روغن کاری شود، تا استفاده از ورق به آسانی میسر شده، آسیبی به آن وارد نشود. در این زمینه، روغن پنبه دانه و یا روغنهای سنتزی مانند دی بوتیل سباسیت (di-butyl sebacate) و یا دی اکتیل سباسیت (dioctyl sebacate)و استیل تری بوتیل سیترات به صورت لایهای بسیار نازک ۵) تا ۲۰
میلیگرم برای هر متر مربع)، بر سطح ورق به صورت فرآیندی الکترواستاتیکی قرار خواهد گرفت. از مواد کاهش دهنده فعالیت سطحی نیز می توان همراه با روغن ها استفاده نمود. پس از انجام تمامی این مراحل، ورقهای متشکل از چندین لایه بدست می اید(شکل(۴که از آن در ساخت قوطی مصرفی صنایع بستهبندی موادغذایی استفاده خواهد شد.
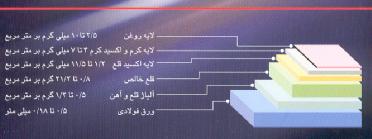
شکل -۴ لایه های تشکیل شده بر روی ورق فولادی پس از قلع اندود شدن گاهی ورقهای قلع اندود تحت عناوین انواع J و K در بازار دیده میشوند که در آنها قلع به صورت
۵/۸ / ۲/۶ g/m2 و یا بیشتر بر روی ورقه فولادی تثبیت شده، تا مقاومت خوبی را نسبت به خوردگی از خود نشان دهند. تفاوت آنها در اندازه بلورهای قلع، مقاومت در برابر اسید میباشد.
محصولات جانبی قلع اندود نمودن ورق
ورق کروم اندود الکترولیتی (electerolytic chromium coated steel) که به فولاد عاری از قلع (tin-free steel) نیز معروف است، از محصولات جانبی کارخانه ورق قلعاندود است که در آن سطح ورق فولادی با دو لایه کروم فلزی و اکسید کروم پوشانده شده است (شکل.(۵ در این روش ۵۰ تا ۹۰ میلیگرم کروم فلزی و ۷ تا ۳۵ میلیگرم اکسید کروم برای هر متر مربع ورق، استفاده میشود:
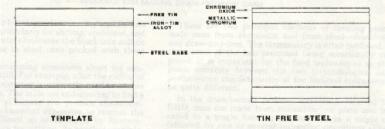
شکل-۵ مقایسه ورق قلع اندود با ورق عاری از قلع این ورقها قبل از مصرف در کارخانه قوطیسازی باید لاک زده شود زیرا لایه اکسیدکروم باعث
سایش شدید ماشینآلات میگردد از ورق کروم اندود الکترولیتی در ساخت قوطیهایی که نیاز به جوشکاری ندارند و نیز انواع درپوشها استفاده میشود.
بازیابی ورق قلع اندود
به دلیل خواص مغناطیسی فولاد، جمعآوری و ذخیره قوطیهای قلع اندود جهت بازیابی، آسان و اقتصادی است. بازیابی هر تن قراضه ورق قلع اندود، ۱/۵ تن سنگ آهن، ۶۶۵ کیلوگرم زغال سنگ، ۱۹۱
کیلوگرم سنگ آهک صرفهجویی را به دنبال دارد. پوشش قلع مشکلی در فرآیند بازیابی ایجاد نمیکند زیرا درصد قلع در قراضه ورق قلع اندود بسیار پائین است. آلاینده های آلی مانند برچسب و رنگ نیز در دمای بیش از ۱۶۰۰ درجه سانتیگراد فرآیند فولادسازی میسوزند.
وزن مبنا (Base weight) و جعبه مبنا (Base box)
وزن مبنا نمادی است که نشانگر ضخامت اسمی ورق میباشد و جعبه مبنا، سطحی معادل با تعداد مشخصی ورق با ابعاد معین است. جعبه مبنا، سطح ۱۱۲ ورق قلع اندود به طول ۲۰ و عرض ۱۴ اینچ است که معادل ۳۱۳۶۰ اینچ مربع خواهد شد. این تعداد ورق با این مشخصات میتواند دارای وزنهای متفاوتی باشد که با توجه به ثابت بودن تعداد ورقها و طول و عرض آنها، تنها متغیر، ضخامت میباشد. به عنوان مثال وقتی وزن مبنا
۴۵ پوند (حدود ۲۱ کیلو گرم) باشد، ضخامت ۱۱۲ ورق ۲۰×۱۴) اینچ) برابر با ۰/۰۰۵ اینچ ۱۲۷) میکرومتر)
خواهد بود. در صورتی که وزن مبنا، به ۱۰۰ پاوند ۴۵) کیلوگرم) افزایش یابد در اینصورت ضخامت هر یک از
۱۱۲ ورق، حدود ۲۸۰ میکرومتر است. در همین زمینه میتوان وزن هر فوت مربع از این ورقها را نیز بدست آورد. با توجه به اینکه ۳۱۳۶۰ اینچ مربع (مساحت کل ۱۱۲ ورق) معادل با ۲۱۷/۸ فوت مربع است، بنابراین در
مثال اول خواهیم داشت:
۱۴×۲۰×۱۱۲ = ۳۱۳۶۰ In2
۳۱۳۶۰ ÷ ۱۴۴ = ۲۱۷/۸ Ft2 ۴۵ ÷ ۲۱۷/۸ = ۰/۲۰۶۶ lb
یعنی که یک فوت مربع از ورق، وزنی برابر با ۰/۲۰۶۶ پوند ۹۴) گرم) خواهد داشت. جدول ۱،
ضخامت را با توجه به وزن مبنا نشان میدهد. در ارتباط با همین ویژگی، واحد دیگری به نام system ) SITA international tinplate area )که معادل یکصد مترمربع است را می توان تعریف نمود. در این حالت تعداد ورقها به جای ۱۱۲، ۱۰۰ عدد در نظر گرفته میشود و سپس SITA از رابطه ذیل بدست خواهد آمد:
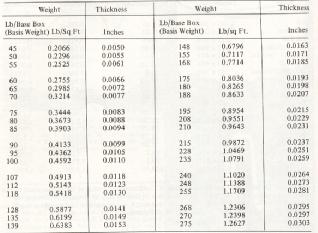
(mm) طول ورق | (mm) عرض ورق |
تعداد ورقها × ـــــــــــــــــــــــ | × ـــــــــــــــــــــــ SITA = |
۱۰۰۰ | ۱۰۰۰ |
در صورتی که هدف تعیین SITA برای کلاف باشد از معادله ذیل استفاده میشود:
(mm) عرض ورق
(m)طول × ـــــــــــــــــــــ SITA =
۱۰۰۰
ــــــــــــــــــــــــــــــ
٢m ١٠٠
-۹
خوردگی
همه ساله تعداد بیشماری از قوطیهای تهیه شده از ورق قلع اندود جهت بستهبندی موادغذایی مورد استفاده قرار میگیرند که در معرض حملات شیمیایی متعددی نیز قرار میگیرند. برخی از محصولات، قلع را مورد حمله قرار میدهند که البته حذف قلع به این شکل قابل قبول به شمار می اید زیرا که این عمل، تحت تاثیر قرار گرفتن ورق فولادی را به تأخیر میاندازد. این عمل با توجه به ضخامت کم قلع و اینکه در برخی نقاط و تحت تاثیر عوامل مختلف همین پوشش ناچیز ممکن است به خوبی تأمین نشده و یا در حین ساخت قوطی از بین رفته باشد، بسیار شایان توجه است. هرگونه حمله به بخش فولادی ورق قوطی میتواند منجر به سوراخ شدن آن شود. در کنار آن باید توجه نمود که اگر تحت تاثیر قرار گرفتن قلع باعث بد رنگ شدن و یا بروز عطر و طعم نامطبوع در محصول میشود، دیگر این عمل مطلوب نبوده و باید از لعاب استفاده گردد.
خوردگی اصولا نوعی پدیده الکتروشیمیایی است که در آن الکترونها جابجا و یا منتقل میگردند.
هرگاه دو فلز غیرمشابه در آب و یا محلولهایی که قابلیت هدایت الکتریسیته را دارند (الکترولیتها) غوطهور شوند و سپس به یکدیگر وصل گردند، آنگاه نوعی سلول گالوانیک بدست خواهد آمد. پتانسیل الکتریکی که به این ترتیب بین دو فلز برقرار میشود، زمینه انتقال الکترونها را از طریق سیم رابط مهیا خواهد ساخت.
در این حالت، دو فلز را الکترود نامیده که یکی کاتد و دیگری آند می باشند و جریان تولید شده بواسطه حرکت الکترونها از آند به کاتد خواهد بود. با حرکت الکترونها از آند، آن قسمت از فلز که در مایع غوطهور است بصورت یونهای مثبت و محلول در می ایند و بنابراین به تدریج آند در الکترولیت حل میشود. در قوطیهای قلع اندود، دو فلز قلع و فولاد که در تماس با یکدیگر هستند در ماده غذایی غوطهور میباشند که همچون یک الکترولیت عمل مینماید.
در این حالت قلع را اگر آند و فولاد را کاتد در نظر بگیریم، آنگاه قلع شروع به حل شدن در ماده غذایی (الکترولیت) نموده، در حالیکه، فولاد به صورت دست نخورده باقی میماند. در این حالت به قلع »آند فدا شونده« میگویند . زیرا با حل شدن خود، فولاد را حفظ میکند (شکل .(۶
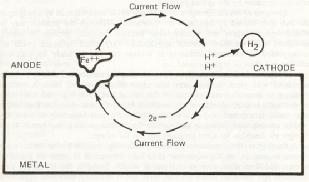
یکی از مهمترین نکات و عواملی که باید کنترل شود، اکسیژن است. معمولا مقدار اکسیژن در قوطیها
کم است و تحت این شرایط، قلع به صورت آندی و فولاد به صورت کاتدی عمل مینمایند که حالت مطلوب به شمار می اید. در صورتی که غلظت اکسیژن بالا باشد. در این حالت قلع به صورت کاتد و فولاد به صورت آند در می ایند و به این ترتیب این فولاد است که سریعا در غذا حل میشود و معمولا باعث سوراخ شدن قوطی میگردد. در همین رابطه پولاریزه شدن نیز اتفاق میافتد. عبور جریان الکتریکی از محلول الکترولیتی منجر به تشکیل گاز هیدروژن در الکترود منفی خواهد شد. قسمت اعظم این گاز خارج میشود اما بخشی از آن به صورت حباب، کاتد را در برگرفته و باعث میشود تا جریان معکوس درآید. در مبحث خوردگی، هر چیزی که از شدت جریان بکاهد، سرعت و شدت خوردگی را نیز کم میکند. بالعکس، هر عاملی که پولاریزه شدن را کم نماید، باعث تسریع خوردگی خواهد شد.
از همین جاست که میتوان دریافت که چگونه اکسیژن محلول در ماده غذایی باعث افزایش خوردگی میگردد. در صورتی که مقدار اکسیژن زیاد باشد، میتواند با ئیدروژن جمع شده در کاتد واکنش داده، پولاریزه شدن را کاهش داد و مجددا جریان اولیه که منجر به خوردگی میشود را ایجاد نماید. فلزاتی که الکترودها را تشکیل میدهند، نقش و اثر مهمی را در خوردگی ایفا مینمایند. فلزات را از نظر تمایل آنها به حل شدن در الکترولیت و تشکیل یون میتوان طبقهبندی نمود.
این سری از فلزات که تحت عنوان »الکتروموتیوها« دستهبندی شدهاند، با عنصر سدیم که به راحتی وارد محلول میشود آغاز و با فلزاتی چون طلا و پلاتین که به هیچ روی حل نمیشوند، خاتمه مییابد. هرچه فلزات از یکدیگر فاصله بیشتری را در این سری داشته باشند، ولتاژ بیشتری در مقایسه با فلزات نزدیک به هم تولید مینمایند. آلومینیوم و آهن در این سری از یکدیگر کاملا فاصله دارند و بنابراین استفاده از دربهای آلومینیومی بر روی بدنه قوطیهای فولادی توصیه میشود، البته با این شرط که این دو با یک پوشش مناسب از هم جدا شده باشند، زیرا در غیر این صورت آلومینیوم سریعا دچار خوردگی می شود.
صرف نظر از عوامل گفته شده و عواملی چون pH و رطوبت، عوامل دیگری چون خوردگی ناشی از تنش (تنشهای بوجود آمده در حین ساخت قوطی و یا انجام کشش شدید بر روی دیواره قوطی)، وجود عوامل بازدارنده خوردگی که گاهی به الکترولیت اضافه میشوند را میتوان نام برد. معمولا تشکیل نوعی لایه اکسید فلزی بر روی فلز میتواند از حل شدن آن جلوگیری نماید که در واقع نوعی حالت روئین برای آن بوجود آورد.
ترکیب شیمیایی ورق فولادی و قلع
مهمترین نکته در ترکیب شیمیایی فولاد، مقدار کربن آن است که باید بسیار پائین باشد زیرا در غیر این صورت، فولاد حاصل به شدت شکننده بوده، فاقد خواص مورد نیاز در بستهبندی است.
ترکیب شیمیایی فولاد شامل عناصر متفاوتی چون منگنز، کربن، فسفر، گوگرد، مس، نیکل، کروم بوده و صرف نظر از مقدار کربن، مقدار فسفر و مس نیز در استفاده از فولاد تاثیرگذار است. در حال حاضر چند نوع فولاد در جهان جهت بستهبندی مورد استفاده قرار میگیرند که در جدول ۲ دیده میشوند.
فولاد نوع L دارای مقدار بسیار کمی فسفر است و برای فراورده هایی که خاصیت خورندگی شدید دارند (با اسیدیته بالا) مانند میوه های تیرهرنگ، ترشیها توصیه میشود. فولاد نوع MR که مقدار بیشتری فسفر نسبت به فولاد L دارد برای محصولاتی با اسیدیته ملایم مانند آب میوه های گلابی، هلو و آناناس مناسب است و در مواردی مانند گوشت و ماهی و اکثر سبزیجات، قابل مصرف می باشد..
جدول -۲ ترکیب شیمیایی چند نوع فولاد پایه مصرفی جهت قلع اندود نمودن
L |
MS |
MR |
MC |
|
نوع فولاد | ||||
منگنز | ۰/۶-۰/۲۵ | ۰/۶-۰/۲۵ | ۰/۶-۰/۲۵ | ۰/۶-۰/۲۵ |
کربن | حداکثر۰/۱۲ | حداکثر۰/۱۲ | حداکثر۰/۱۲ | حداکثر۰/۱۲ |
فسفر | ۰/۰۱۵ | ۰/۰۱۵ | ۰/۰۲ | ۰/۱۱-۰/۰۷ |
گوگرد | ۰/۰۵ | ۰/۰۵ | ۰/۰۵ | ۰/۰۵ |
سیلیس | ۰/۰۱ | ۰/۰۱ | ۰/۰۱ | ۰/۰۱ |
مس | ۰/۰۶ | ۰/۱ | ۰/۲ | ۰/۲ |
نیکل | ۰/۰۴ | ۰/۰۴ | – | – |
کروم | ۰/۰۶ | ۰/۰۶ | – | – |
مولیبدن | ۰/۰۵ | ۰/۰۵ | – | – |
آرسنیک | ۰/۰۲ | ۰/۰۲ | – | – |
فولاد نوع MC که در آن مقداری فسفر به ترکیب اضافه شده است نیز برای محصولاتی که خاصیت خورندگی نداشته و یا اثر کمی دارند مناسب است و به جهت داشتن استحکام برای ساخت قوطیهای سه قسمته بکار میرود. فولاد نوع N که بیشتر برای قوطیهای کششی و درب قوطیهای آئروسول مناسب است و از نظر ترکیب شیمیایی شبیه به فولاد نوع L بوده که به آن تا ۰/۰۲ درصد نیتروژن افزوده شده تا بدین ترتیب سختی و مقاومت به کشش فولاد افزایش یابد. ترکیب شیمیایی قلع با درجه A (ممتاز) در جدول۳ دیده میشود. بطور کلی تمامی ناخالصیهای موجود در این نوع قلع کمتر از ۰/۲ درصد است، ضمن آنکه در روش الکترولیتی تقریبا قلع خالص بر روی فولاد تثبیت میشود.
جدول -۳ درصد عناصر همراه با قلع (ناخالصیها)
عناصر |
% |
قلع (حداقل) | ۹۹/۸ |
آنتیموان (حداکثر) | ۰/۰۴ |
آرسنیک (حداکثر) | ۰/۰۵ |
بیسموت (حداکثر) | ۰/۰۱۵ |
کادمیوم (حداکثر) | ۰/۰۰۱ |
مس (حداکثر) | ۰/۰۴ |
آهن (حداکثر) | ۰/۰۱۵ |
سرب (حداکثر) | ۰/۰۵ |
نیکل (حداکثر) | ۰/۰۱ |
گوگرد (حداکثر) | ۰/۰۱ |
روی (حداکثر) | ۰/۰۰۵ |
-۱۱
ساخت قوطی از ورق فولادی قلعاندود (حلبی)
از انواع مختلف قوطی جهت بستهبندی موادغذایی استفاده میگردد که عبارتند از:
الف: قوطی سه تکهای
در این حالت ابتدا ورق به اندازه های معینی که جهت ساخت قوطی مورد نظر لازم است در می اید. در بخش ساخت بدنه بر روی دو انتهای این ورقها شکافها و بریدگیهایی (notching) ایجاد میگردد (شکل۷
بخش (۱ که سپس به صورت قلاب در می ایند (شکل۷، بخش۲و ۳ و ۴و .(۵ حالت دندانهدار موجود باعث میشود که عمل لحیمکاری راحتتر صورت گیرد. پس از آنکه بدنه استوانهای شکل ساخته شد، قسمت درز از روی شعله عبور داده میشود تا بدین ترتیب مواد مذاب بتوانند کاملا در محل این درز قرار گیرند. در مرحله بعد یک لایه از لعاب به سطح داخلی و خارجی محل اتصال پاشیده میشود. مراحل بعد به ترتیب ایجاد لبه قلاب مانند (flang) (شکل۷ بخش (۶ در دو سر استوانه و نیز چیندار (beading) نمودن بخش استوانهای جهت افزایش مقاومت آن به ضربه است.
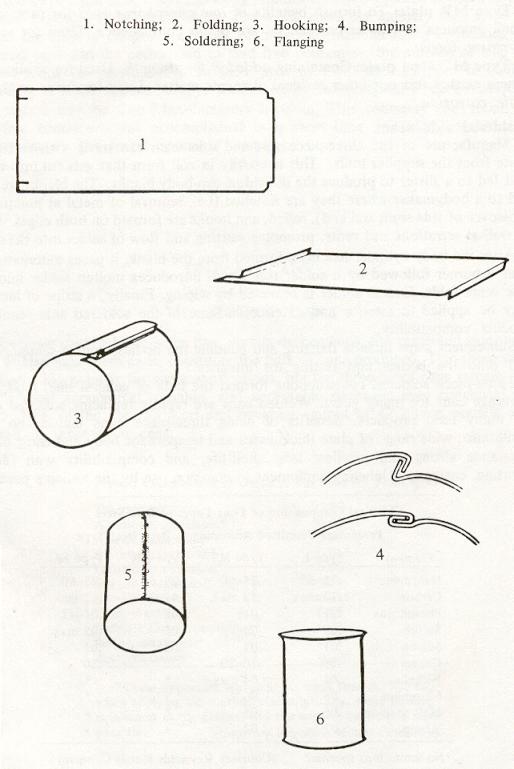
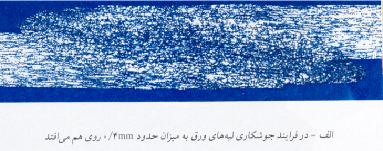
قوطیه ای سه قسمته را به روش جوشکاری نیز میتوان تهیه نمود. در این حالت، ابتدا لبه های ورق که
به شکل استوانه درآمده روی یکدیگر قرار میگیرند. (شکل.(۸ جریان الکتریسیته همراه با فشار بر ناحیهای که همپوشانی لبه ها صورت گرفته، اعمال میگردد. اگر جنس ورق قوطی از فولاد قلع اندود باشد، از سیم مسی جهت کمک به انتقال جریان برق استفاده میگردد ولی اگر جنس ورق فولادی عاری از قلع باشد از الکترودهایی که مانند غلطک بوده و ضمن حرکت و ایجاد فشار الکتریسیته را نیز عبور میدهند، استفاده میشود(شکل.(۹ این روش بر روش لحیم کاری مزیت و برتری دارد زیرا اولا از مواد لحیم کاری (مثلا سرب)
استفاده نمیشود، ثانیا، درز جانبی از ضخامت بسیار کمی برخوردار است و بنابراین در رنگآمیزی بدنه قوطی مشکلی ایجاد نمینماید. از طرف دیگر دوام بیشتر نسبت به درزهای لحیمکاری شده دارد.
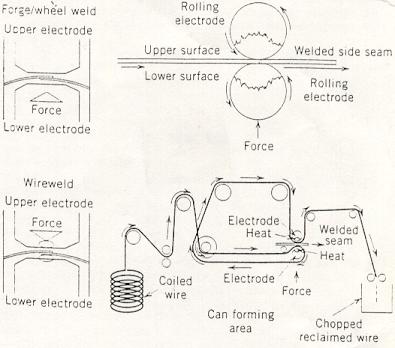
ب: قوطی دو تکه ای
این نوع قوطی از دو قسمت بدنه و درب فوقانی تشکیل شده است و بدنه و کف یک پارچه است و توسط فرآیند کشش تولید میگردد و قسمت سر قوطی پس از پرکردن با موادغذایی، به بدنه دوخته میشود.قوطی دو تکهای شامل دو نوع کششی (شکل های ۱۰ و (۱۲ و کششی عمیق (شکل(۱۱ است. در نوع کششی قوطیها با ارتفاع کمتر از نصف قطر قوطی تهیه میشوند و تنها یک مرحله پرس مورد نیاز است . در صورتی که قوطی با ارتفاع بیشتری مورد نیاز باشد، طی چند مرحله کشیده میشود. در این قسمت استفاده از مواد روانساز بسیار ضروری است. در هر حال روش کشش عمیق را میتوان برای انوع ورقهای فلزی (که قبلا
در مورد آلومینیوم ذکر شد) بکار برد و از مزایای مهم آن حذف درز جانبی است.
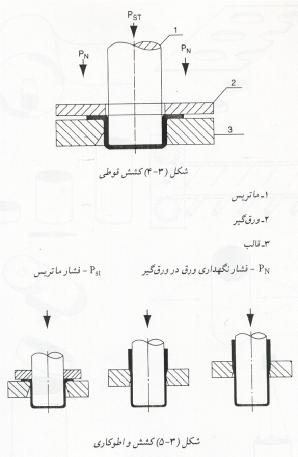
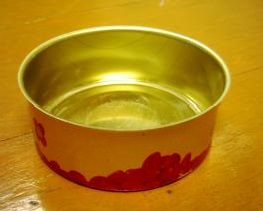
ج: قوطیهای قابل اسپری یا آئروسول
بخش اعظم این نوع قوطیها از ورق قلعاندود ساخته میشود، گرچه آلومینیوم را نیز میتوان در تهیه آنها بکار گرفت. بخشهای مختلف دارای ضخامتهای متفاوتی است. ورق بدنه نازکترین بخشهاست و ضخامت آن بین ۰/۱۸ تا ۰/۳۸ میلیمتر متغیر است و بستگی به قطر قوطی دارد. حالت فوق زمانی است که قطر بین ۴۵ تا ۵۲ میلیمتر باشد. در صورتی که قطر بین ۵۷ تا ۷۶ میلیمتر باشد از ضخامت ۰/۲۱ تا ۰/۴۴ استفاده میگردد. قسمتهای فوقانی و تحتانی جهت جلوگیری از بیرونزدگی و باز شدن قلابها و در نهایت انفجار، دارای ضخامت بیشتری هستند. بدنه این نوع قوطی نیز به روش کشش عمیق تولید می شود (شکل .(۱۳
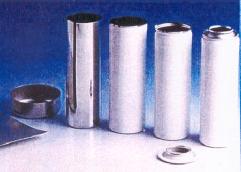
Valve cup، معمولا از ورقی با ضخامت ۰/۲۶۶ میلیمتر ساخته میشود. قوطیهای آئروسول را میتوان قوطی چهار قسمته دانست زیرا علاوه بر کف و بدنه دارای دو قسمت درب فوقانی گنبدی شکل و Valve cupاست. (شکل-۱۴الف). بر روی قسمت اخیر والو (شکل-۱۴ب) قرار میگیرد که با فشار دادن آن، فضای
داخلی قوطی از طریق یک مجرا به فضای اتمسفر راه پیدا مینماید و در مواردی مثلا پاشیدن روغن به سطوح بسیار مناسب است. صرفنظر از موادغذایی که در درون قوطی قرار میگیرد (به عنوان مثال، روغن یا خامه) از یک گاز به عنوان حامل موادغذایی نیز باید استفاده گردد، در این زمینه از گازهایی چون بوتان، ایزوبوتان و پروپان بهره برده میشود. استفاده از گازهای فشرده مانند دیاکسیدکربن و نیتروژن نیز معمول است، اما چون معمولا خیلی سریع خارج شده بنابراین بخشی از ماده غذایی در درون قوطی باقی مانده و امکان خروج آنها وجود نخواهد داشت.
ب
الف
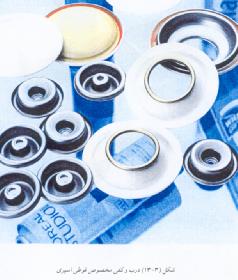
درجه سختی
(Temperness)
درجه سختی ورقهایی که نورد سرد را گذرانده و سپس به دو روش جعبهای (box) و یا مداوم
(continous)، تنش زدایی شدهاند نقش تعیین کننده در خصوصیات و کاربرد ورق ها دارد. جدول۴ این خصوصیات را نشان میدهند. درکنار آن انجام نورد مضاعف نیز میتواند بر همین عوامل موثر باشد.
لعابها و پوشش های روی ورق قلعاندود
استفاده از لعابهای آلی به منظور جلوگیری از انجام واکنش بین موادغذایی و سطح داخلی قوطی میتواند مفید واقع گردد. در مواردی که البته چندان زیاد نمیباشد استفاده از قوطیهایی که فاقد لعاب بوده و در آنها ماده غذایی درتماس با قلع میباشند نیز مناسب میباشد. قلع خاصیت رنگبری داشته و میتواند باعث بهبود رنگ محصولاتی شود که اگر در قوطیهای لعابدار بستهبندی شوند رنگ آنها تیره میشود. لعابهای مورد استفاده برای پوشش سطح داخلی قوطیهای قلع اندود را میتوان به چند نوع تقسیم نمود که عبارتند از:
الف: الئورزینها
معمولترین انواع لعابها بوده و شامل نوع «R» یا لعابهای میوهای و نوع «C» هستند. نوع «R»
بطورمشخص برای حفاظت از رنگیزه میوه هایی که از رنگ زیادی برخوردار هستند (آلبالو، چغندر) بکار میرود. نوع «C» برای جلوگیری از بد رنگ شدن محصولاتی مانند ذرت، نخودفرنگی، ماکیان و غذاهای دریایی که اصطلاحا»۲سولفید سیاه« نامیده میشود، بکار میرود و حاوی ۱۵ درصد اکسید روی بوده که به عنوان یک جزء شیمیایی و نه به عنوان رنگیزه به رزین افزوده میشود. سولفیدهایی که در حین فرآیند و یا در زمان استریل کردن در فرآورده غذایی حاوی اسیدهای آمینه گوگرددار بوجود می ایند با اکسید روی ترکیب شده و مشتقات سفید یا بیرنگ روی را بوجود می اورند. این نوع پوشش، در ابتدا برای کنسروهای ذرت بکار گرفته شد و به corn enamel موسوم بود و بعدها به پوششهای نوع «C» تغییر نام داد. از اولئورزینها معمولا در قوطیهایی که در آنها فرآورده های اسیدی بستهبندی میشوند استفاده میگردد.
ب: فنولیکها
در قوطی غذاهای دریایی و برخی انواع گوشت بکار میرود و نفوذ ناپذیری بیشتر نسبت به اولئورزینها دارد هرچند انعطافپذیری خوبی نداشته و حتی طعم و مزه خاصی را در غذا ایجاد میکنند. جهت مقاومت در برابر رنگ سولفیدی نیازی به استفاده از اکسید روی در ترکیب آنها نمیباشد و تحت تاثیر چربیهای حیوانی نرم نمیشوند.
ج: اپوکسیها
مقاومت بسیار خوبی به حرارت دارند بطوری که در نواحی مجاور درز که عملیات لحیمکاری صورت میگیرد، دچار تغییر رنگ نمیشوند. انعطافپذیری بسیار خوبی داشته و میتوان از آنها برای ساختن دو انتهای قوطیها استفاده نمود. هیچ گونه عطر و طعم را در موادغذایی ایجاد ننموده و از این نظر بعد از وینیلها قرار میگیرند. اپوکسیها را میتوان با افزودن فنولیکها تعدیل نموده و از آنها برای بستهبندی محصولاتی مانند میوه ها و غذاهای پرچربی استفاده نمود.
د: وینیلها
این لعابها بصورت مضاعف همراه با اولئورزینها و یا اپوکسی بکار میروند و در غذاهایی که خاصیت خورندگی بالایی داشته باشند، مورد استفاده قرار میگیرند. یک نمونه آن استفاده از لایه وینیل بر روی لایه R در قسمت درز جانبی قوطیهایی است که برای بستهبندی عصاره سیب بکار میروند. وینیلها، لعابهای مستحکمی بوده و عاری از طعم و بو هستند. این لعابها گرچه مقاومت خوبی به بخار آب ندارند، اما حرارتهای تا حدود ۹۵ درجه سانتیگراد و کمتر را به خوبی تحمل مینمایند. از دیگر انواع لعابها، میتوان به وینیل تعدیل شده با اپوکسی و اپوکسی تعدیل شده با فنولیک و فنولیکهای تعدیل شده اشاره نمود که به ترتیب برای بستهبندی میوه های دارای رنگ فراوان و محصولات گوشتی استفاده میشوند. برای لعاب دادن ورقه های قلعاندود، سطوح توسط پوشش دهنده های غلطکی لعاب خورده و سپس در درجه حرارت ۲۰۰ تا ۲۳۵
درجه سانتیگراد پخته میشوند. میتوان لعابها را به درون قوطی و یا هر یک از بخشهای آن نیز اسپری نمود.
همانگونه که ذکر شد، عدم استفاده از لعاب میتواند در مواردی مفید باشد که این امر منسوب به اثر رنگ بری قلع است. از جمله این محصولات میتوان به کنسرو کلم شور (sauerkraut)، آب گریپفروت، کنسرو گلابی و یا هلو، آناناس و پرتقال اشاره نمود.
ه : پلیمرهای پلیپروپلین و پلی اتیلن تری فتالات (PET)
از این دو پلیمر نیز جهت لعاب دادن ورقه های فولادی قلع اندود استفاده میگردد. این پلیمرها به یکی از سه روش ذیل بر روی ورق قرار میگیرند (شکل.(۱۵
روش : A استفاده از حرارت و بدون استفاده از هر نوع چسب. در این حالت دمای ورق بیشتر از نقطه
ذوب پلیمر (PET) است و پلیمر ذوب شده از حالت بلورین به صورت بیشکل (amorph) در می اید.
روش : B پلیمر با چسب آغشته شده و سپس روکش دهی انجام میگیرد و در آن دمای ورق کمتر از نقطه ذوب پلیمر (PET) میباشد و معمولا یک سطح ورقهای کروم اندود را با آن میپوشانند و سطح دیگر با لعابها و رزینها آغشته خواهد شد.
روش : C نوار ورق به چسب آغشته شده و سپس با PET یا PP پوشانده میگردد.
لعابها معمولا بر حسب مورد در ضخامت ۰/۰۰۲۵ تا ۰/۰۱۲۷ میلیمتر به کار میروند و بین ۳ تا ۹ گرم از آنها برای پوشش هر متر مربع ورق قلع یا کروم اندود مصرف خواهد شد.
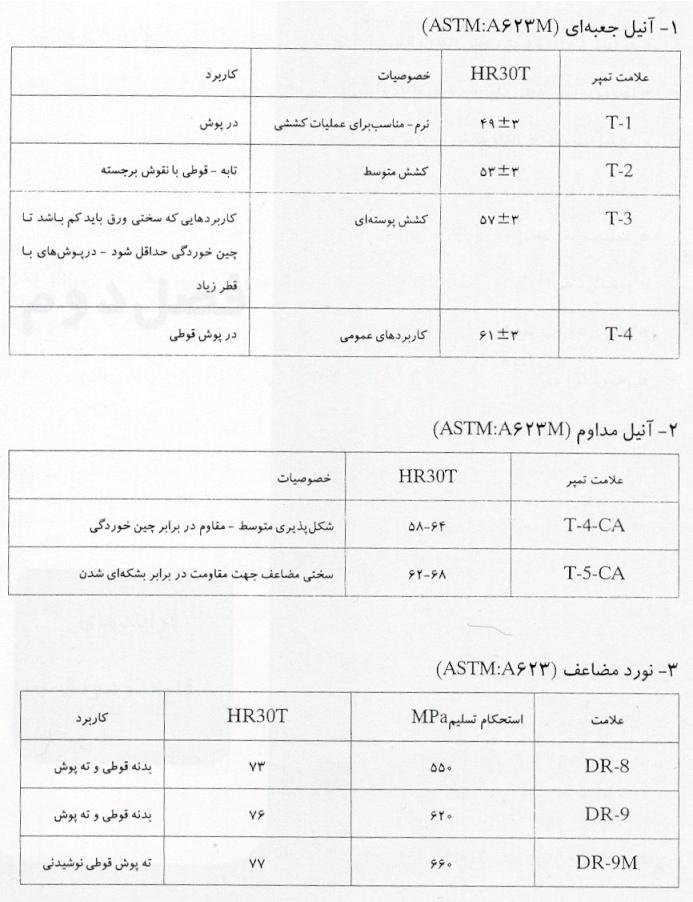
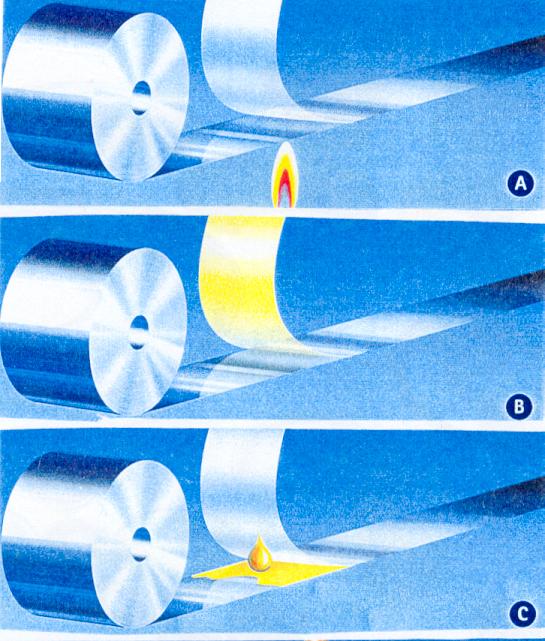
فولاد و مایکروویو
با توجه به اینکه امواج ماکرویو امکان عبور از فولاد را ندارند بنابراین به سوی ماگنوترون بازگشته می توانند باعث اتش سوزی گردند.
چند اصطلاح رایج در صنعت تهیه ورق (قلعاندود)
: Temper designation -1 میزان سختی ورقهایی که یک بار توسط نورد سرد ضخامت آنها کاهش یافته و نشان دهنده خواص شکلگیری آنها میباشد
: Burr -2 برآمدگی در سطح ورق (حداکثر ۰/۰۵ میلیمتر قابل قبول است).
: camber -3 میزان انحناء در کناره های ورق و در هر متر ۱/۳ میلیمتر قابل قبول است.
: matte finish -4 جلای مات که پس از تثبیت قلع به روش الکترولیتی و قبل از سفیدگری دیده میشود. : cross bow -5 نوعی انحناء متقاطع که در طول ورق دیده میشود.
: feather edge -6 تفاوت ضخامت ورق در عرض آن است و در فاصله ۶ میلیمتر و ۲۵ میلی از لبه ورق اندازهگیری خواهد شد. تفاوت این دو نباید از ۱۵ درصد (ضخامت موردنظر) تجاوز نماید.
: crown -7 تفاوت ضخامت ورق در مرکز عرض ورق و ۱۰ میلیمتری لبه ورق را گویند.
: out-of-square -8 میزان انحراف لبه دو ورق از خط راست هنگامی که با زاویه قائمه بر روی یکدیگر قرار میگیرند که در هر سوی نباید از ۱/۵ میلیمتر بیشتر باشد.
: steel density -9 که برای ورقهای فولادی مناسب جهت قلع اندود نمودن ۷۸۵۰ kg/m3 میباشد g/cm3)
.(۷/۸۵
: nominal tin coating weight -10 مقدار قلعی که بر روی سطوح ورق فولادی قرار میگیرند که معمولا اندکی کمتر از مقدار واقعی است.
: differentially coated tin plate -11 نشان دهنده تفاوت در میزان قلع تثبیت شده بر هر سطح فولاد است. مثلا
D 5/6 / 2/8 ، حرف D نشان دهنده تفاوت میزان قلع در هر سطح، عدد سمت چپ، نشان دهنده میزان قلع در سطح خارجی یا بالائی و عدد سمت راست نشان دهنده میزان قلع در سطح داخلی (زیرین) میباشد.
در مواردی از هارد باکس میتوان برای بسته بندی مواد غذایی استفاده کرد که نیاز به ماندگاری طولانی ندارند و برای هدیه استفاده می شوند.