چوب (MDF)
چوب قرنهاست که جهت بستهبندی مورد استفاده قرار مـیگیـرد. مـاده ای اسـت کـه مـیتـوان آن را بـه راحتی شکل داده و بهم متصل نمود و بر حسب منبع مـیتوانـد از اسـتحکام خـوبی نیـز برخـوردار باشـد. چـوب حاصل از جنگل به صورت الوار، خاک اره یا ترکه ای بوده که به محصـولات متفـاوتی چـون تختـه چنـد لایـه، نئوپان (که از تکه های اره کاری بدست می آید)، خمیر کاغذ، کاغذ و مقوا تبدیل می گـردد. در برخـی از نقـاط دنیا از چوبهای ترکه ای هنوز هم برای ساخت انواع سبد و جعبه استفاده میگردد.
معمولا از چوبهای نـرم جهـت تولید بسته استفاده می گردد و این امر تحت تأثیر نوع درخت و چوب حاصل از آن میباشد. در جدول ۱ درختها بر حسب ارجحیت به چهار دسته تقسیم شده اند که با نزدیکتر شـدن بـه گـروه چهـار ارجحیـت و برتـری چـوب کاهش مییابد.
الوارهای چوبی که جهت استفاده و ساخت جعبه به کار میروند باید به خوبی خشک شـوند بگونـه ایـی که رطوبت آنها به حدود ۱۵-۲۰ درصد برسد. خشک کردن یک مرحله آماده سازی بسیار مهم در ایـن صـنعت به شمار می آید زیرا که از بروز تغییرات شـدید ناشـی از جمـع و یـا متـورم شـدن مـیکاهـد، چـوب را از حملـه میکروب ها در امان نگه می دارد، وزن را کاهش می دهد، قدرت و استحکام چوب را بیشتر می کند و بالاخره آن را برای انجام عملیات بعدی همچون پرداخت آماده می سازد.
خشک کردن یا در محیط صورت مـیگیـرد و یـا در محفظه های کنترل شده (از نظر درجه حرارت و میزان رطوبت) که به روش اخیر Kiln drying گفته میشـود و می تواند در مدت کوتاهی ۲) تا ۵ روز) رطوبت چوب را بـه حـدود ۱۶ درصـد برسـاند حـال آنکـه روش اول ممکن است بین ۲۰ تا ۳۰ روز طول بکشد. . ذکر این نکته ضروری است که به دلایلـی چـون در دسـترس بـودن نیروی کار ارزان قیمت، قیمت پائین و وجود منابع جنگلی فراوان استفاده از جعبه هـای چـوبی در کشـورهای در حال توسعه بیشتر معمول میباشد. در جدول ۲ خواص تعدادی از چوبهای مصرفی جهت تولیـد جعبـه نشـان داده است.
کرده است
جدول -۱ چوبهای مورد استفاده جهت تهیه جعبه
Group 4 | Group 3 | Group 2 | Group 1 |
Beech | Black ash | Agba | Alpine fir |
Birch | Black gum | Douglas fir | Aspen |
Hichory | Maple | Hemlock | Basswood |
Osk | Red gum | Larch | Cedar |
Rock elm | Sycamore | Gaboon | Chestnut |
White ash | White elm | Lime | Cottonwood |
Obeche | Jack pine | ||
Lodge polepine | |||
Norway pine | |||
Spruce | |||
White pine | |||
White fir | |||
White pine | |||
Willow | |||
Yellow |
در هر حال الوار (Timber) و یـا کنـده (Log) حاصـل از جنگـل را مـیتـوان بـه صـورت تختـه چنـدلا
(Plywood) و یا فیبر (Fibre boards) در آورد، هرچند که قسمت عمده آن بدون هیچ گونـه فرآینـدی پـس از
بریده شدن در اندازه ها و قطعات موردنظر، جهت ساخت جعبه به کار میرود.
جدول
خواص چوبهای مورد استفاده جهت تهیه جعبه
چروکیدگی حجمی |
دانسیته |
Species |
||
(%) | ||||
۱۵ | ۰/۷۱ | Oak (Quercus alba) | ||
۱۸ | ۰/۶۸ | |||
Beech(Fagus sylvatica) | ||||
۱۴ | ۰/۶۱ | |||
Birch(Betula verra cosa) | ||||
۱۲ | ۰/۴۹ | |||
Pine (Pinus sylvesteris) | ||||
۱۲ | ۰/۴۳ | |||
Spruce (Picea abies) |
فرآیند ساخت تخته چندلا را می توان در شکل ۱ مشاهده نمـود. الـوار پـس از حمـل بـه کارخانـه، ابتـدا پوستگیری میشود و آنگاه قسمتهای زائد در دو انتها بریده میگردد .(Trimming)
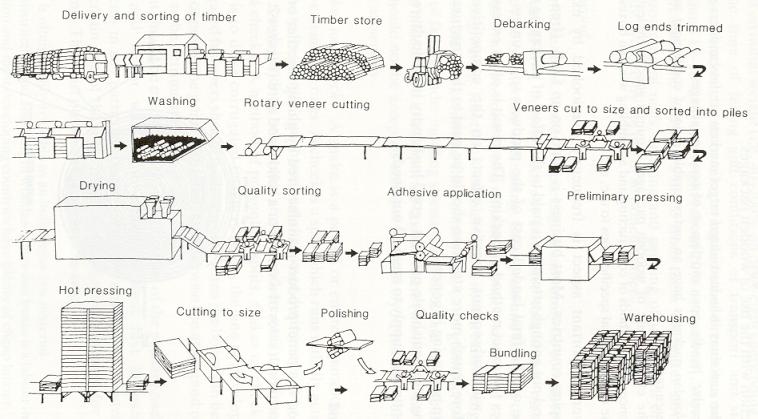
ضمن چرخش توسط یک تیغه ی بسیار نازک به ورقهای بسیار نازک
(Veneer) تبدیل میگردند (شکل .(۲ این ورقهای نازک پس از آنکه در اندازه های معین در آمدند، خشک شده و برحسب مورد توسط چسب تعدادی از آنها به هم چسبانده شده، بـه صـورت گرمـاگرم تحـت فشـار قـرار کرده است می گیرند تا جهت ساخت جعبه هارد باکس استفاده گردند. در ساخت فیبر، ضایعات حاصل از ارهکاری و قطعـات کوچـک باقیمانده از الوارها، به صورت قطعات کوچک (chips) در میآیند. این قطعات سپس توسـط بخـار و فشـار نـرم شده و به آن آب اضافه می گردد تا تشـکیل خمیـر بدهـد.
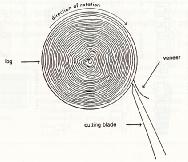
در ایـن مرحلـه ممکـن اسـت مـوادی چـون سـولفات آلومینیوم به خمیر اضافه گردد. این خمیر توسط توریهای سیمی به آرامی به هـم زده مـی شـود تـا حالـت الیـافی بدست آید. در مرحله بعد پس از خارج کردن آب، خمیر مرطـوب از میـان غلطـک هـایی عبـور کـرده و بـدین ترتیب الیاف در یکدیگر ادغام می گردند و در نهایت توسط آون کاملا خشک می شوند. یکی از اقداماتی که به هنگام ساخت جعبه های سخت ام دی افی از فیبر ممکن است صورت پذیرد خم نمودن فیبر است کـه معمـولا از نیـروی فشـار اسـتفاده می گردد هرچند که نمی توان به شعاع کمتر از ۳۰۰ میلی متر برای لایه فیبر با ضخامت ۳/۲ میلیمتر دسـت یافـت.
برای حصول به شعاع کمتر (مثلا۱۲۵ ۲ میلیمتر) باید فیبر را مدتی در آب خیساند.
کاغذ و مقوا سخت
مواد اولیه
از اواسط قرن نوزدهم میلادی صنعت کاغذ شروع به استفاده از خمیر چوب جهت تولیـد ایـن محصـول نمود و همین امر باعث شد تا بدین ترتیب بشر شروع به بهرهبرداری از جنگلها بنماید که اکنـون منجـر بـه بـروز مشکلات زیست محیطی شده است. به هر روی در این زمینه ضمن این که صنعت تولیـد کاغـذ بـه دنبـال ایجـاد نوعی توازن بین برداشت از جنگل و احیای جنگل است، شروع به استفاده از منابع دیگر مانند پنبه، الیاف بـزرک
(flax) و اسپارتو (esparto) و خیزران جهت تولید کاغذ نموده است، هرچند که هنوز هم چوب درختان اولین و مهم ترین منبع الیاف های سلولزی به شمار می آیند. صرف نظر از چوب، از چندین ماده غیر سلولزی دیگر جهت تولید کاغذ استفاده می شود که از آن جمله می توان به املاح، جهت پوشش دادن، رنگها و موادی که چوب را به نفوذ آب مقاوم مینماید اشاره کرد. این مواد را اصولا میتوان در چهار دسته ردهبندی نمود:
الف ـ پرکننده ها: که رنگیزه های معدنی سفید رنگ مانند خاک چینی هستند که ماتی و در عین حـال براقیـت را در کاغذ ایجاد نموده، سطح آن را کاملا صاف و آماده چاپ میکنند.
ب ـ مت ل کننده ها (قوام دهنده ها): که شامل نشاسته، صمغهای گیاهی، رزینهای سنتزی میشـوند و اسـتحکام کاغذ را در مقابل پارگی، کشش و ترکیدن افزایش میدهند.
ج ـ ترکیبات ایجاد حالت آهار :
(Sizing) که باعث میشوند تا کاغذ نسبت به مایعات مانند آب یا مرکب چـاپ مقاوم گردند و به همین دلیـل اسـت کـه کاغـذ خشـککـن هـا (blotting papers) فاقـد ایـن ترکیبـات هسـتند.
کاغذهای مخصوص تحریر دارای آهار بوده هرچند که میزان آهار متفاوت می باشد و بر این مبنا بـه دو صـورت نرم و سخت دیده میشوند. جهت آهار زدن کاغذ از امولسیونهای مومی و رزین استفاده میگردد.
د ـ افزودنیهای متفرقه: مانند پیگمان های رنگی جهت تولیـد کاغـذ رنگـی، صـمغ جهـت سـهولت شـکلدهـی، ترکیبات ضد کف و مواد ضد رطوبت.
گفته شد که چوپ ماده اولیه عمده تولید کاغذ است. تنه درخت از دو لایـه پوسـت داخلـی و خـارجی تشکیل شده که در زیر آن لایه رشد که حاوی موادغذایی لازم جهت رشد گیـاه اسـت، وجـود دارد(شـکل .(۳
پس از این سه لایه، بخش اصلی و چوبی تنه که شامل دسته های متعددی از الیاف سلولزی است، دیده مـی شـود که به صورت عمودی توسط ماده ای به نام لیگنین ( lignin) کنار هم قرار گرفته اند. بخش چوبی از نظر ترکیـب شیمیایی شامل ۵۰ درصد الیاف سلولزی، ۳۰ درصد لیگنین، ۱۶ درصد کربوهیدرات و ۴ درصد ترکیبـاتی ماننـد پروتیینها، رزین ها و چربی است. الیاف سلولزی همین قسمت است که جهت تولید کاغذ استفاده می گردد. این الیاف که باریکتر از تار موی انسان میباشند تنها دارای چند میلیمتر طول بوده و لیگنین این الیاف را در کنار هم نگه میدارد و نوعی عمل چسب را انجام میدهد.
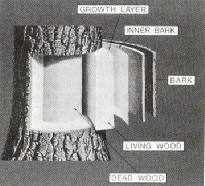
فرآیند تولید خمیر کاغذ
مهمترین نکته در این فرآیند آن است که خواص یک کاغذ یا مقوا به شدت تحت تأثیر خواص خمیر تهیه شده از چوب میباشد. خمیر را میتوان به دو روش مکانیکی و شیمیایی و با استفاده از چوبهای سخت (پهن برگها) و یا چوبهای نرم (سوزنی برگها) تهیه نمود. خمیر حاصله ممکن است بدون انجام عمل رنگبری و یا پس از انجام آن مورد استفاده قرار گیرد.
الف : تهیه خمیر به روش مکانیکی
کاغذ به دست آمده در این روش از وزن بالا، استحکام پایین و البته قیمت نه چندان بالا برخوردار است و از آن جهت بستهبندی کمتر استفاده میشود. در این روش الوارهـای بـدون پوسـت چـوب بـه بلنـدی ۱/۲ متـر توسط غلطک های زبر آسیاب و رنده می شوند، تا به قطعاتی در حدود ۱۵-۲۰ میلـیمتـر درازا برسـند. از جریـان آب نیز بهره گرفته می شود تـا بـدین ترتیـب الیـاف سـلولزی بیشـتر جـدا شـوند (شـکل .(۴ در ایـن روش صـرفا
ناخالصی های محلول در آب جدا می شوند و بخش اعظم لیگنین در خمیر باقی مـی مانـد ضـمن آنکـه بخشـی از الیاف به صورت دسته باقیمانده و بخشی نیز دچار آسیب می گردند. از این خمیر برای تهیه کاغذ روزنامه استفاده میگردد و گاهی نیز با خمیر حاصل از روش شیمیایی مخلوط شده، به مصرف تولید مقوا میرسد.
ب : تهیه خمیر به روش شیمیایی
این روش با قطعات کوچک و رنده شده (chips) کار خود را شروع می نماید و سپس با استفاده از مواد شیمیایی لیگنین را به صورت محلول در میآورد که پس از شستن خارج خواهد شد (شکل .(۵
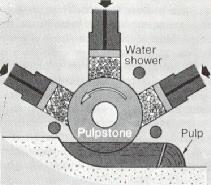
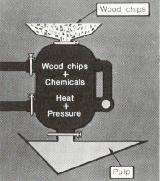
این روش الیاف را با خلوص بیشتری تولید میکند و آسیب دیدگی الیاف کمتر بوده و حالت دستهای به ندرت دیده می شود. روش شیمیایی را می توان به چند نوع انجام داد و کیفیت خمیر حاصله بستگی بـه نـوع ایـن فرآیندها و نوع فیبر چوب مصرفی دارد. برای تولید کاغذ مناسب جهت بسته بندی، سـه روش شـیمیایی اسـت از اهمیت بیشتری برخوردار هستند که شامل فرآیند کرافت (kraft) که استحکام الیاف بـه خـوبی حفـظ مـیشـود، فرآیند سولفیته که از استحکام کمتری برخوردار است و بـالاخره فرآینـد نیمـه شـیمیایی اسـت. فرآینـد کرافـت دارای سابقه ای بیش از ۱۰۰ سال است و خمیر معمولا بدون انجام عمل رنگبری مورد اسـتفاده قـرار مـی گیـرد و راندمان تولید بسیار خوب و بالایی دارد. در صورتی که هدف تولید کاغذ سفید به این روش باشد، ضمن انجـام عمل رنگبری، بخشی از استحکام کاغذ بدست آمده از دست می رود. در فرآیند کرافت، خـرده چـوب توسـط محلولی از سود سوزآور و سولفات سدیم برای چندین ساعت هضم می گردد.
در این شرایط لیگنین هضم شـده و جدا می گردد. وجود سـولفات سـدیم باعـث مـی شـود کـه در حـین فرآینـد، سـولفید سـدیم تولیـد گـردد. بـا جمع آوری سولفید سدیم و سـپس اسـتفاده مجـدد از آن در درجـه حـرارت و فشـار بـالا، سـود سـوزآور تولیـد می گردد که کار هضم را به انجام خواهد رساند.
علت نامگـذاری ایـن روش بـه کرافـت آن اسـت کـه در زبـان سوئدی کرافت به معنی »قوی« میباشد. اولین نمونه های کاغذ بدست آمده به این روش بیشتر بـه رنـگ قهـوه ای بوده و در ثانی به دلیل وجود الیاف های بلند که به صورت غیـر یکنواخـت در بافـت کاغـذ توزیـع شـده بودنـد، لکه لکه (blotchy) دیده می شدند.
در روش سولفیته از دی اکسید سولفور و بی سولفیت کلسیم استفاده می گـردد که با خرده چوب در محیط آبی و درجه حرارت ۱۴۰ درجه سانتیگراد مخلوط میگردند. بدین ترتیـب لیگنـین حل شده، جدا میگردد و پس از شستن الیاف با آب، توسط ماده شـیمیایی رنگبـر همچـون هیپوکلریـت کلسـیم رنگبری می گردد با این روش، الیاف سلولزی با خلوص بالا تولیـد مـیشـود، هرچنـد اسـتحکام کاغـذ آن ماننـد روش قبل نخواهد بود. در روش نیمه شیمیایی، خرده چوب تا حدودی به روش مکانیکی و تا حـدودی بـه روش شــیمیایی تیمــار مــیگردنــد. کاغــذ حاصــل از ایــن نــوع خمیــر بیشــتر بــرای تولیــد کاغــذ و مقــوای کنگــرهدار
(corrugated) استفاده میگردد.
تولید کاغذ
پس از تولید خمیر و در صورت نیاز رنگبری، نوبت به فرآیندی به نام »زدن خمیر(beating)« مـی رسـد.
هدف عمده از انجام این عمل مالش دادن و برس زدن الیاف سلولزی است بگونـه ایـی کـه از طـول بـه صـورت کاملا مجزا در آیند تا بعدها بتوان در کاغذ به صورت محکم آنها را کنار هم قرار داد. به این فرآیند الیاف سازی
(fibrillation) گفته شده و هرچه بهتر صورت گیرد، کاغذ از استحکام بیشتری برخوردار خواهد شد.
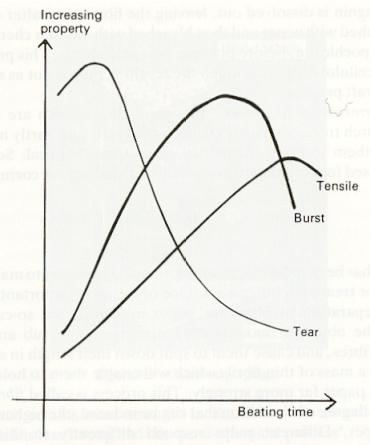
چوبهای نرم در مقایسه با انواع سخت راحت تر فرآیند فوق را تحمل مینمایند و از همین رو از چوبهای نرم کاغذهایی با استحکام بیشتر و کیفیت بهتر میتوان بدست آورد. در این عملیات و بواسطه حرکت تیغه ها، بخشی از الیاف برش خورده و کوتاه میشوند که هرچند باعث کاهش استحکام کاغذ میشوند، اما میتواند در حرکت کاغذ بر روی ماشینهای برش و چاپ تسهیل ایجاد نماید. زدن خمیر تأثیر زیادی بر خصوصیات کاغذ تولید دارد که میتوان این تاثیر را در شکل ۶ مشاهده نمود. خمیر پس از آنکه آماده شد، به ماشینهای ساخت کاغذ منتقل میگردد. این ماشینها که به نام مخترع آنها، فوردراینیر (Fourdrinier) نامیده میشود، از ۸ قسمت اساسی که ۴ بخش مربوط به قسمت مرطوب و ۴ بخش مربوط به قسمت خشک است، تشکیل شده است.
قسمت مرطوب |
قسمت خشک |
stuff box | برس |
head box | خشککن |
برش slice | براقکن |
سیستم فوردراینیر fordrinier | صافکن |
در stuff box یک مخلوط آبکی از خمیر کاغذ حاوی ۹۷ قسـمت آب و ۳ قسـمت خمیـر اسـت امـا از آنجا که تهیه کاغذ از آن آسان نیست در یک مخلوط کن، رقیق شده بگونهای که غلظـت خمیـر بـه ۰/۵ درصـد میرسد و بنابراین ماده مصرفی دارای ۹۹/۵ درصد آب خواهد بود. در head box ، به آرامـی مخلـوط الیـاف و آب بهم زده میشود تا یک سوسپانسیون یکنواخت از الیاف تشکیل گردد.slice یک شکاف باریک در جلوی head box است که از طریق آن مخلوط الیاف و آب بـه صـورت لایـه نـازک بـر روی نقالـه منتقـل مـیشـود و می توان اندازه این شکاف را کم یا زیاد نمود. نقاله فوردراینیر ضمن حمل مواد منتقل شده از شکاف، ایـن مـواد را به غلطکی که کار آن فشردن و به صورت لایه در آوردن خمیر رقیق است (couch)، انتقـال مـیدهـد، ضـمن آنکه خمیر رقیق تا رسیدن به این غلطک مقداری از آب خود را هم از دست میدهد. این عمل توسـط تعـدادی غلطک که در زیر نقاله قرار گرفته و عمل مکش را انجام می دهند تسریع میگردد. در این مرحله، صفحه الیـافی
(fiber mat) هنوز دارای رطوبتی حدود ۷۵-۸۰ درصد است که باید در مرحله خشک کردن جدا شود (شـکل۷ ) . در پایان این مرحله صفحات به قسمت خشک که آن هم دارای ۴ بخش است، انتقال مـی یابنـد. اولـین بخـش پرسها هستند. نحوه انتقال صفحات به این پرس بدین ترتیب است که از نقاله هایی که از جنس نمد (felt) هستند استفاده میگردد.
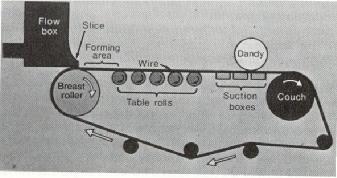
مجموعه نقاله نمدین و صفحات الیافی مرطوب ابتدا از پرس که ممکـن اسـت دارای مکـش و یـا بـدون
که باید در مرحله خشک کردن جدا شود. خشک کن ها، استوانه های گرمی هستند که به شکلی مختصر با کاغذ تماس پیدا کرده و آن را خشک مینمایند. براقکن یا (machine glazed) MG dryer در مـواردی کـه نیـاز بـه مکش باشند عبور می نماید. در پایان بخش پرس کردن صفحات هنوز دارای حـدود ۶۰ درصـد رطوبـت هسـتند
ایجاد جلا باشد استفاده می گردد و شامل غلطکهای سنگین وزن کاملا صافی هستند که با فشـار خـود سـطح را براق می نمایند. در آخرین بخش از قسمت خشک، ماشین هـای مخصـوص فشـرده کـردن (calendering) قـرار دارند که شامل چند غلطک هستند که صرفا غلطک زیرین (آخرین) با نیروی محرکه به حرکـت در مـی آینـد و سایر غلطک ها تحت تاثیر خاصیت اصطکاکی کاغذ حرکت می نمایند. در پایان ایـن بخـش، کاغـذ بـه صـورت یک رول بزرگ در میآید.
کیفیت کاغذ
برای آنکه کاغذ جهت مصارف بسته بندی مناسب باشد بایـد بـه عـواملی ماننـد درجـه بهـم زدن، مقـدار پرکننده، قوام دهنده ها، آهار دهنده ها و نوع فیبر توجه نمود. بخش عمده ای از کاغذ تولیدی جهت بستهبندی بـه صورت ورق (unconverted paper) استفاده مـیشـود کـه در واقـع اسـتفاده از آن بـرای پیچیـدن((wrapping) محصولات است. اما بخش دیگری از کاغذ به اشکال گونـاگون ماننـد ساشـه، پاکـت و کیسـه و ماننـد آنهـا در می آیند. بر حسب اینکه چه عملی را پوشش کاغذی انجام مـیدهـد، دامنـه ای از خـواص را بایـد دارا باشـد کـه میتوان آنها را در دو دسته کلی خواص فیزیکی و شیمیایی دستهبندی نمود.
خواص فیزیکی
الــف-توصــیف کاغــذ: در ایــن مــورد بیــان نــوع کاغــذ و ضــخامت و یــا وزن یــک مترمربــع آن یــا گرامــاژ (grammage)، ضروری است. از آنجا که اسـتحکام کاغـذ بـا افـزایش ضـخامت آن و بـه عبـارت بهتـر وزن آن افزایش مییابد، اندازهگیری وزن میتواند سادهترین معیار برای بیان کیفیت کاغذ باشد.
ب-خواص نوری: شامل رنگ، درجه مات بودن، براقیت و درخشندگی
ج-استحکام: شامل مقاومت به کشش و سوراخ شدن، مقاومت اولیه به پارگی، مقاومت داخلی به پاره شدن.
د-خواص ممانعتی: مانند حساسیت به رطوبت و اکسیژن.
ه-خصوصیات متفرقه: مانند میزان اصطکاک سطحی نشان دهنده سهولت کار با کاغذ در دستگاه های اتوماتیک.
خواص شیمیایی
در صورتی که ماده غذایی در تماس مستقیم با کاغذ است نباید حاوی حتی مقادیر جزیی از موادی باشد که ممکن است بر ماده غذایی موثر باشند، به عنوان مثال کاغذهایی که برای پوشش ظروف فلزی کاملا صیقلی استفاده می شود نباید حالت اسیدی یا قلیایی داشته، عاری از مواد سولفاته و یا سایر ترکیبات عامل خوردگی باشد. همچنین باید عاری از فلزات سنگین و فلزاتی مانند آهن و مس باشند زیرا که اگر مثلا برای بستهبندی کره بکار روند حضور عناصر فوق میتواند اکسیداسیون را آغاز نموده که به ترشیدگی خاتمه مییابد.
انواع کاغذ
الف ـ کاغذ کرافت:
از استحکام خوبی برخوردار بوده و به دو رنگ قهوهایی و سفید تولید میگردد و برای مصارفی مانند تهیه پاکت و یا پیچیدن محصولات غذایی در آنها مناسب است.
ب ـ کاغذهای قابل کشش:
این نوع کاغذ از طریق ایجاد موجهای کوچک عرضی در سطح کاغذ هنگامی که هنوز مرطوب است بدست میآید و میتواند تا حدودی کشش را تحمل نموده و سپس مجددا به حالت اول خود بازگردد.
ج ـ کاغذهای مقاوم پس از مرطوب شدن (wet-strength papers)
کاغذ پس از مرطوب شدن، مقاومت خود را از دست میدهد. بخش عمدهای از استحکام کاغذ بواسطه وجود پیوندهای هیدروژنه بین گروه های هیدروکسیل و کربوکسیل الیاف مجاور است. خارج کردن آب به هنگام ساخت کاغذ این پیوندها را برقرار میکند و بنابراین جذب رطوبت باعث جدا شدن آنها میگردد. این نوع کاغذها که با کاغذهای مقاوم به بخار آب و یا واترپروف متفاوت هستند باید پس از اشباع شدن با آب قادر به حفظ استحکام خود در حد ۳۰ درصد از استحکام کاغذ خشک باشند. برای ساخت این کاغذ، از مواد شیمیایی که قادر به ایجاد پیوند هیدروژنه هستند استفاده میگردد که در این مورد به موادی مانند اوره و رزینهای آمینی اشاره نمود. این مواد به هنگامی که خمیر در حال آماده شدن است اضافه شده و در مرحله خشک کردن تکمیل میشوند. این نوع کاغذ بیشتر برای پوششهای خارجی که در معرض رطوبت بالای محیط هستند مناسب است.
د- کاغذهای مقاوم به چربی و روغن:
در این زمینه کاغذ بر حسب مدت زمان تماس با روغن یا محصول روغنی، با موم و یا رزینهای سنتزی
پوشانده میشود.
ه ـ چرم گیاهی: (Vegetable parchment)
در دو مرحله تولید میشود. در مرحله اول و طبق روش فوردینیر، کاغذ بدست میآید که در مرحله دوم از میان حمام اسید سولفوریک که درجه حرارت و قدرت آن کاملا کنترل شده عبور مینمایند. با غوطهور نمودن کاغذ جاذب در اسید غلیظ، الیاف سلولزی متورم شده، خلل و فرج خود را پوشانده و فضای خالی بین الیاف پر میگردد و بدین ترتیب پیوندهای هیدروژنه زیادی شکل میگیرد و کاغذی به دست میآید که به آب مقاوم بوده، فاقد پرز (lint)، طعم و بو است و به چربی و روغن نیز مقاوم است و وزن آن ۴۰ تا ۷۵ گرم برای هر مترمربع متغیر می باشد.
و ـ کاغذ گلاسه:
با عبور کاغذهای مقاوم به چربی از یک ماشین مخصوص فشرده کردن، سطح کاغذ جلای خاصی دیده و دانسیته آن کاملا افزایش مییابد. ساختار کاملا بهم بافته و هیدراته سلولز در کاغذ گلاسه این امکان را فراهم میآورد تا آن را برای دامنه وسیعی از موادغذایی استفاده کرد. البته کاغذ گلاسه مقاوم به رطوبت نیست و برای جبران این نقیصه باید پوشش دهی صورت گیرد که بدین ترتیب میتوان درببندی با حرارت را نیز انجام داد.
ز ـ کاغذ حریر:
از دسته کاغذهای بسیار نازک و نرم با وزن ۱۷ تا ۳۰ گرم برای هر مترمربع هستند و در مواردی که محصول در معرض خطر خراشیدگی و خشک شدن باشد از آن استفاده میگردد.
کاغذ را می توان به اشکال گوناگون مـورد اسـتفاده قـرار داد. اخیـرا و بـا توجـه بـه افـزایش اسـتفاده از مایکرویو، تولید بسته های کاغذی که سازگاری خـوبی نیـز بـاAِسیسـتم فـوق دارنـد آغـاز شـده اسـت. محتـوای بسته های کاغذی را به راحتی می توان در صورت نیاز در مایکروویو فرآیند نمود. بسته های Popcorn که بعـد از قرار گرفتن در دستگاه مایکرویو به صورت پف کرده در می آینـد و همزمـان حجـم بسـته کاغـذی نیـز افـزایش مییابد، از این دسته به شمار میآیند (شکل .(۱۱
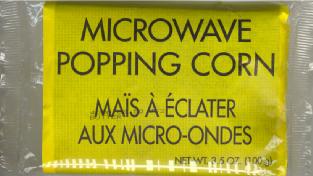
تولید مقوا
مقوا از موادی است که به شکل گستردهایی جهت بستهبندی بکار میرود. بر اساس تعریف ISO در صورتیکه کاغذ دارای وزن ۲۵۰ گرم در هر مترمربع (۲۵۰ g/m2) یا بیشتر باشد، آن را مقوا مینامند. مقوا عمدتا
از الیاف سلولزی حاصل از چوب تهیه شده است. ساختار مقوا میتواند از یک لایه یک دست (y) تا ۲ الی ۸
لایه تشکیل شده باشد. لایه فوقانی معمولا از خمیر چوبی که به روش شیمیایی تهیه شده و رنگبری گردیده است، میباشد. در زیر این لایه، یک لایه با کیفیت پایین ولی رنگ روشن وجود دارد تا از دیده شدن رنگ خاکستری یا قهوهای، لایه های میانی جلوگیری نماید. خواص ساختار مقوا بسیار شبیه به آنچه در مورد کاغذ گفته شده بوده و خواص اختصاصی آن بیشتر تابع تعداد لایه های بکار رفته است. رگه یا الیاف در آن به صورت (MD) machine diredion یعنی هم جهت با حرکت ماشین است و کمتر از نوع (CD) cross direction و
عمود بر MD است. بنابراین استحکام نوع MD آن بیشتر میباشد. از نظر خواص سطحی، بستگی بسیار به عملیاتی دارد که بر روی لایه فوقانی و تحتانی صورت گرفته است. خواص نوری آن نیز شبیه به کاغذ است و همانگونه که ذکر شد باید جهت جلوگیری از بد رنگ شدن، یک لایه روشن زیر لایه فوقانی در نظر گرفته شود. نحوه ساخت آن نیز شبیه به کاغذ است و از ماشین فوردراینیر استفاده میگردد. با توجه به اینکه تهیه لایه ضخیم در این ماشین دشوار است، تنها راه حل ساخت لایه های نازک و سپس متصل کردن آنها به هم است. در زمینه ساخت مقوا میتوان از قالبهای استوانهای (شکل( ۸ نیز استفاده کرد که در این حالت استوانه گرم در درون یک ظرف حاوی خمیر رقیق در حال چرخش بوده و با قرار گرفتن لایه نازکی از خمیر رقیق بر روی آن، در نهایت به صورت ورقه نسبتا ضخیم خارج میگردد. برای آنکه بتوان به صورت همزمان، چند لایه را تولید و بر روی هم قرار داد میتوان تعدادی از ماشینهای فوردراینیر را پشت سر هم قرار داد و یا آنکه یکی از این ماشینها را در کنار یک یا چند قالب استوانه ای مورد استفاده قرار داد.
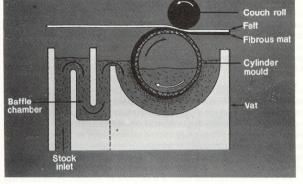
از نظر انواع مقوا ممکن است به صورت ساده (plain) باشد که در آن هیچگونه تیمار بر روی سطح انجام نگرفته و در مواردی که نمایش بسته اهمیت چندانی ندارد استفاده میگردد خاصیت چاپپذیری خوبی نداشته از استحکام زیاد برخوردار نیست. نوع دیگر، مقوای با رویه سفید است که علاوه بر ظاهر مطلوب، قابلیت چاپ و تاخوردگی را به خوبی دارا است و بیشترین مصرف را در بین مقواها دارد. سطح داخلی آن چندان جذاب نبوده و بنابراین از این مقوا در مواردی که ظاهر سطح داخلی از اهمیت برخوردار نیست استفاده میگردد.
گاهی در اثر پرکردن قوطیهای ساخته شده از این نوع مقوا با آرد یا محصولات حاوی روغن لکه هایی بر روی سطح داخلی ایجاد میگردد که در این موارد استفاده از کیسه های پلاستیکی توصیه میشود. اگر کارتن ساخته شده از این مقوا، به صورت مکرر باز و بسته شود در این صورت برای آنکه ظاهر مقوا در قسمت داخلی نیز بهتر شود، باید از مقوایی که دو رویه آن سفید است (duplex board) استفاده نمود.
از دیگر انواع مقوا باید مقوای حاصل از خمیر خالص را (pure pulp board) نام برد که برای آرد، محصولات قنادی و شکلات که احتمال نشت روغن و ایجاد لکه میرود استفاد میشود. در این نوع مقواها، آن را با لایه ای از کاغذ ضد چربی و یا کاغذهای موسوم به چرم گیاهی و یا کاغذ گلاسه پوشش میدهند.
مقوای دارای لایهای از موم مقوایی است که میتواند در صنایع بستهبندی موادغذایی استفاده شود و بیشتر از آن برای بستهبندی محصولات منجمد و سرد بهره برده میشود. اخیرا به جای موم از ترکیبات پلیاولفینی به صورت روکش استفاده میگردد.
یکی از تمهیداتی که در جهت افزایش مقاومت مقوا خصوصا نسبت به ضربه انجام میگیرد، قرار دادن یک لایه کنگرهدار (corrugated) یا چین خورده (fluted) بین دو یا چند لایه کاغذ است و ممکن است ۱ تا ۳
لایه باشد که با افزایش مقدار آن مقاومت مکانیکی مقوا نیز افزایش مییابد. جهت چیندار کردن مقوا، آن را از میان غلطکهای گرم همراه با جریان بخار عبور میدهند. بخار مقوا را نرم کرده و قابل چین خوردن مینماید.
مقوای نرم سپس از غلطکهای کنگرهدار عبور نموده و ضمن آن بر سطح فوقانی آن چسب اضافه میشود. در همین زمان یک لایه کاغذ بر روی مقوای چین خورده قرار داده میشود (شکل.( ۹ امروزه مقواهای کنگرهدار بر حسب تعداد چینها و ارتفاع هر چین به چهار دسته A و B و C و E که به ترتیب درشت، ریز، متوسط و بسیار ریز هستند تقسیم میگردند. (جدول .( ۳ از انواع A ، B و C در مصارف صنعتی استفاده میگردد، حال آنکه نوع E بیشتر در مواردی که ظاهر بسته از اهمیت بسیاری برخوردار باشد معمولا با کاغذ دارای کیفیت چاپ بسیار خوب پوشانده میگردد.
جدول ۳ انواع مقواهای چین خورده | |||
کد مقوا | تعداد | ارتفاع هر | میزان تحمل به نیرو |
درشت (A) | ۱۰۴-۱۲۵ | ۴/۵-۴/۷ | ۱۴۰ |
ریز (B) | ۱۵۰-۱۸۴ | ۲/۱-۲/۹ | ۱۸۰ |
متوسط (C) | ۱۲۰-۱۴۵ | ۳/۵-۳/۷ | ۱۶۵ |
بسیار ریز (E) | ۲۷۵-۳۱۰ | ۱/۱۵-۱/۶۵ | ۴۸۵ |
کاغذهایی که جهت چیندار کردن مورد استفاده واقع میشوند میتواند، کاغذهایی چون آنچه به روش نیمه شیمیایی بدست آمده، کاغذ حاصل از الیاف نی و خیزران، کاغذ کرافت و بالاخره کاغذ حاصل از ضایعات باشد. در مورد کاغذهای روکشدهنده (liners) که جهت پوشش چینها استفاده میگردد، معمولا از کاغذ کرافت رنگبری نشده و یا سایر کاغذهای با کیفیت نسبتا پائین استفاده می شود. جدول ۴ گراماژ این کاغذها را نشان میدهد. چیندار کردن به شکل محسوسی مقاومت را افزایش میدهد. گذشته از آن میتوان با استفاده از روش ایجاد »اتصالات عرضی« و بکارگیری الیافی که در آنها اتصالات عرضی هم بوجود آمده است، به استحکام مقوا افزود.
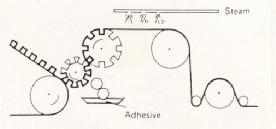
در روش تهیه کاغذ اصولا الیاف به صورت موازی هم و موازی جهت ماشین تولید کاغذ در میآیند و بنابراین اگر از آنها جهت تولید قوطی استفاده گردد، در مقابل فشارهای عمودی مقاومت چندانی از خود نشان نمیدهند که برای رفع آن، دو روش مورد استفاده قرار میگیرد:
در حالت اول لایه های کاغذ به صورت مورب روی هم قرار داده میشوند (شکل( ۱۰ که به این ترتیب الیاف نیز به صورت مورب قرار گرفته و بنابر این از استحکام بیشتری برخـوردار خواهنـد بـود. در تکنولـوژی جدیـدتر از کاغذهایی که برخی از الیاف آن با زاویه ۹۰ درجه در کنار الیاف موازی واقع شدهاند، استفاده شده است.
جدول ۴ وزن کاغذهای مورد استفاده جهت پوشش لایه های چینخورده (گراماژ) g/m2 | ||||||
کاغذ | گراماژهای در دسترس | |||||
کرافت | ۱۲۵ | ۱۵۰ | ۲۰۰ | ۲۵۰ | ۳۰۰ | |
خیزران | ۲۰۰ | ۲۵۰ | ۳۰۰ | ۰۰ | ||
تک لایه | ۱۲۵ | ۱۵۰ | ۲۰۰ | ۵۰ | ||
معمولی | ۱۱۵ | ۱۷۵ | ۲۰۰ |
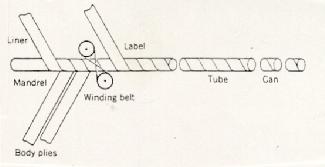
انواع بسته های مقوایی
گذشته از قوطی های مقوایی که طرز ساخت آن بیان گردید و معمولا دارای درب های فلزی (آلومینیوم و یا فولاد قلع اندود) در بخش های فوقانی و تحتانی هستند و حتی می توان انها را تحت خلا نیز در آورد، (شکل
(۱۲ مقوا را می توان به صورت انواع کارتن های کوچک و بزرگ در آورد که انواع کوچکتر به شکل وسـیعی به عنوان بسته اولیه کاربرد دارند(شکل .(۱۳
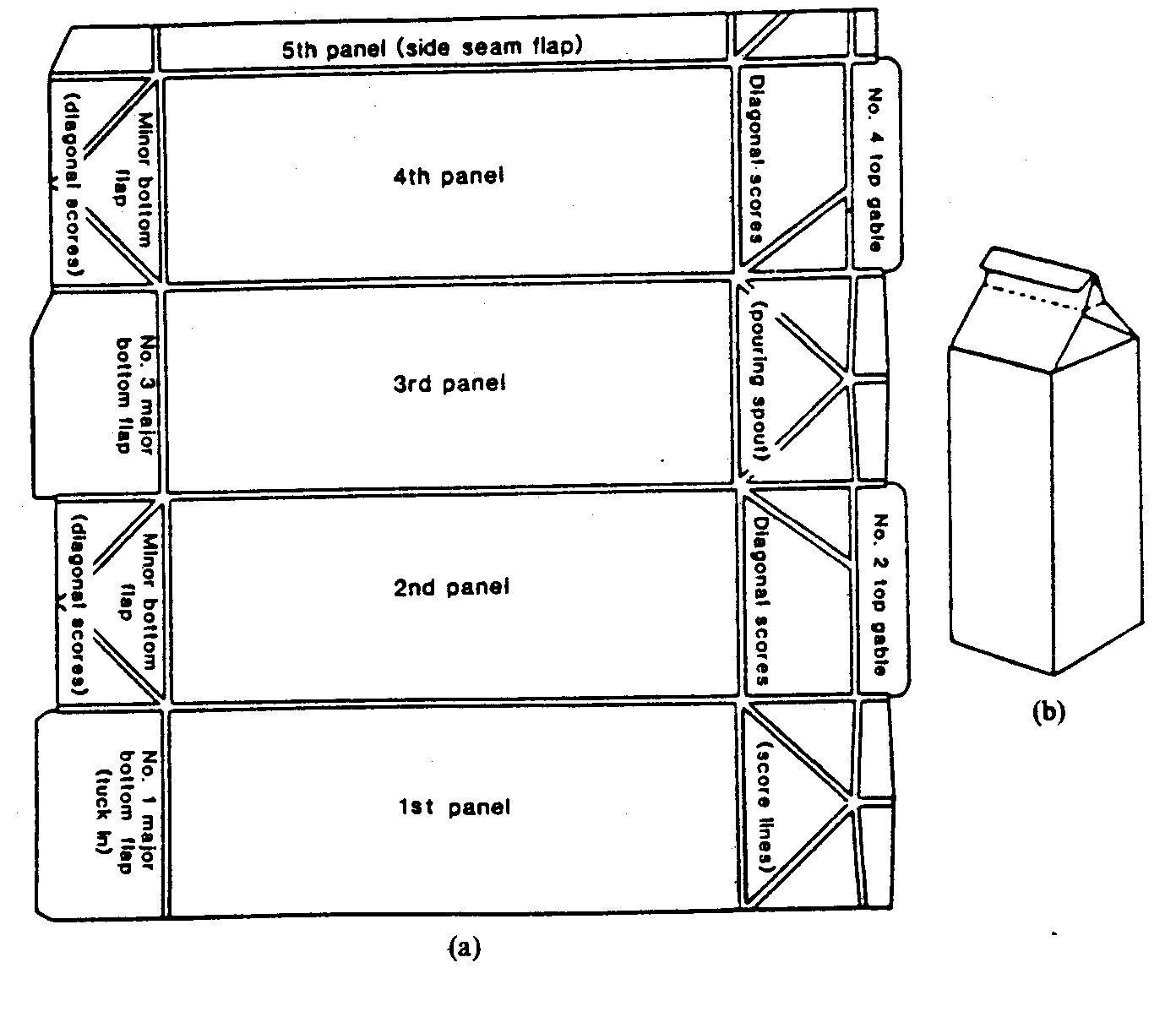