شیشه قرن هاست که در اختیار بشر قرار گرفته است. در ابتدا، کاربرد ساده ای داشته و از آن جهـت تهیـه ظروف آبخوری، تنگهای آب و مانند آن استفاده شده و میشود (شکل (۱ اما اکنون مادهای است که در صنعت تکنولوژی کاربرد بسیار وسیعی دارد. مثال ها در این زمینه، حباب لامپ ، فایبر گلاس، فیبر نوری و شیشـه جـام می باشند. شیشه اما هنوز بیشترین کاربرد را بعنوان یک ماده اولیه جهت بسته بندی مواد غذایی داراسـت، بطـوری که، نقش خود را بشکل موثری حفظ نموده است. عوامل متعددی در بکارگیری ظروف شیشه ای دخالت داشـته بعنوان مزایا نسبت به بسته بندی جعبه هارد باکس برای آن بشمار میآیند که از آن جمله میتوان به موارد ذیل اشاره نمود:
۱ – شفافیت
یکی از مهمترین مزایای ظروف و بستههای شیشهای، شفافیت آنها است و بـدین ترتیـب مصـرف کننـده قادر خواهد بود تا قبل از خرید فراورده، محتوی آن را مورد بررسی قرار دهد و به این ترتیب ضروری است کـه محتویات بسته های شیشه ای استانداردهای لازم حداقل از نظـر ظـاهر را دارا باشـند. اسـتفاده از ظـروف شیشـه ای شفاف به تشخیص و هدایت مشتریان کمک می نماید.
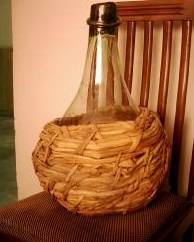
۲- استحکام
گرچه شیشه یک ماده شکننده است، اما هنگامی که استحکام آن به عنوان مثال از نقطه نظر بار عمـودی
(head load) بررسی شود، دارای کیفیت قابل ملاحظهای است. شیشه در حالتی که تحت فشار باشد نیز مقاومت بسیار خوبی از خود نشان می دهد، هرچند مقاومت آن به کشش چندان قابل توجه نیست. شیشه ماننـد یـک مـاده الاستیک از خود رفتار نشان می دهد و می تواند مقداری انرژی را در خود جذب نمایـد. ایـن خاصـیت خصوصـا هنگامی که ظروف شیشه ای با ضخامت نه چندان زیاد ساخته می شوند از اهمیت بالایی برخوردار است. طراحـی نیز عاملی خواهد بود که مقاومت به فشار را تعدیل نموده، باعث توزیع یکنواخت آن در درون ظرف خواهد شد.
۳- شکل پذیری
شیشه یک ماده ترموپلاستیک است که تقریبا۲ دارای نقطـه ذوب مشخصـی نمـی باشـد. تصـویر شـماره ۲
بطور شماتیک تغییرات ویسکوزیته تحت تأثیر حرارت در مورد شیشه و فلز را نشان میدهد.
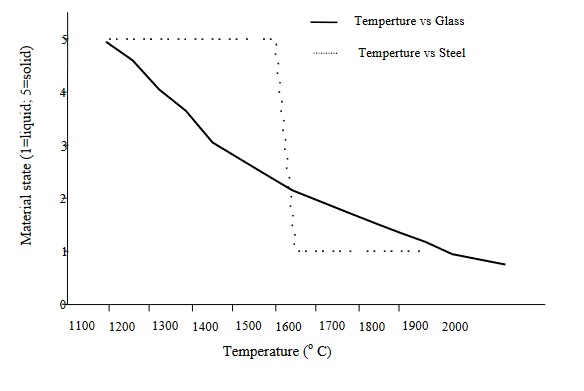
شکل -۲ رفتار شیشه و فولاد در مقابل درجه حرارت بالا همانگونه که ملاحظه میگردد فلزات ابتدا مقاومت بالایی را به درجه حرارت نشان داده و سـپس سـریعا در یک درجه حرارت خاص ذوب شده و در نتیجه ویسکوزیته بشدت کاهش مییابـد. در مـورد شیشـه کـاهش ویسکوزیته تدریجی بوده و بدلیل همین تدریجی بودن تغییرات است که شکل دهی بـه آن توسـط ابـزار مناسـب براحتی امکان پذیر می باشد، بگونهائی که می توان بسته هایی که از نظر شکل نیـز تـداعی کننـده محصـول هسـتند (مثلاعسل در بسته های شبیه خرس یا کندو) را تولید نمود.
ظروف شیشه ای ظروفی میان تهی بوده و بسـیار شـبیه به ظروف فلزی دو قسمتی می باشند و از این رو فاقد هرگونه درز جانبی یا انتهایی هستند. با توجه به اینکه ایجـاد شیار بر روی سطح خارجی شیشه در قسمت های فوقـانی کـه جهـت درب بنـدی مـورد نیـاز مـی باشـد (finish)
بسادگی میسر است، بنابراین از این نظر نیز شیشه دارای مزیت نسبی میباشد.
۴- ترکیب شیمیایی و واکنش ناپذیری
ترکیب مواد اولیه مصرفی جهت تولید ظرف شیشه ای به گونهای است که آن را به کلیه مواد غذایی اعم از جامد یا مایع و یا گاز مقاوم می سازد و بدین ترتیب هیچگونه پوشش داخلی مورد نیاز نمیباشد. تنها اسـتثنا در این زمینه تاثیر مواد قلیایی قوی است که در البته در صنایع بسته بندی موادغذایی کـاربرد نـدارد. همچنـین گـاهی مواد حساس به قلیا بهتر است که در ظروف شیشهای بسته بندی نگردند که این مورد هـم بیشـتر در مـورد برخـی داروها و یا فرآورده های خونی صدق می نماید.
به هرروی در صورت نیاز از فرآیند سولفاته کردن جهت زدودن یون های سدیم از سطح شیشه استفاده می گردد. . بدلیل ثبات شیمیایی آنها را می توان بدون آنکه دچـار هـر نـوع تخریب سطحی شوند، در یک دوره طولانی نگهداری نمود
۵- مقاومت حرارتی
تمامی ظروف شیشه ای پس از سـاخته شـدن در درجـه حـرارت نزدیـک بـه ذوب مجـددا۲ حـرارت داده می شوند ( ۵۴۰–۵۷۰ °C ) تا بدین ترتیب فرآیند استرس زدایی در آنهـا انجـام شـود، از ایـن رو مـی تـوان انتظـار داشت که این ظروف براحتی درجه حرارت های پاستوری شدن، سترون سـازی و حتـی شـوک هـای حرارتـی (
برنامه های گرم و سرد کردن) را تحمل نمایند. در این زمینه مقاومت آن را براحتی می توان با افزودن مـوادی بـه ترکیب اولیه شیشه مثلااکسید بور ( boric oxide) مانند آنچه در ظروف بوروسیلیکات ( با نام تجـارتی (pyrex
دیده میشود، بشکل محسوسی افزایش داد.
۶- نفوذ ناپذیری
شیشه به تمامی گازها و بخار آب نفوذناپذیر است و بعنوان مثـال نشـت گـازCO2 مصـرفی جهـت تولیـد نوشابه های گازدار در عمل صفر میباشد.
۷- رنگ
هرچند اکثر ظروف شیشه ای بصورت بیرنگ و شفاف ساخته میشوند، امـا مـیتـوان بـدلایل مختلـف و بسادگی رنگ شیشه را به سبز، کهربایی، شیری رنگ، قهوه ای و … نیز تغییر داد. با توجه به ضرورت اسـتفاده از رنگ در مواردی مانند بسته بندی شیر، ماء الشعیر و یا نوشابه های بدون رنگ (up-type) اهمیت تولید رنگ بیشتر آشکار می گردد. جهت ایجاد رنگ در شیشه، از مقادیر جزئی مواد و ترکیبات شـیمیایی همچـون اکسـید کـروم (برای رنگ سبز)، آهن، گوگرد و کربن (جهت تولید رنگ زرد کهربایی) و اکسید کبالـت (بـرای رنـگ آبـی) استفاده می شود.
در صورتی که هدف تولید بلور یا شیشه های بدون رنگ باشد رنگ برهایی مانند سلنیوم، نیکـل و کبالت به خمیر شیشه اضافه میگردد.
۸- قابل برگشت بودن
در این زمینه هزینه های اقتصـادی نقـش مهمـی را ایفـا مـی نماینـد، هرچنـد نیازمنـد وجـود سیسـتم هـای جمع آوری و حمل و نقل مناسب است. علاوه بر این در بحث ساخت شیشه به اثری که اسـتفاده از خـرده شیشـه
(cullet) در کاهش موثر مصرف انرژی دارد نیز اشاره خواهد شد.
۹- قابلیت استفاده مجدد
در بسیاری موارد حتی اگر ظروف قابل برگشت نباشند، می توان از آنها مجددا۲ استفاده نمود آنچنان کـه در منازل بشکل گسترده ای معمول است. برخی از تولیدکنندگان گاهی بسته هـای شیشـه ای را بگونـه ای طراحـی می کنند که با خرید محصـول، نـوعی جـایزه نیـز نصـیب مشـتریان خواهـد شـد. مثـال در ایـن مـورد بسـته بنـدی شکلات های صبحانه ای و یا عسل در بستههای لیوانی شکل است. این نکته را هم می توان افزود که بـا توجـه بـه ایمن بودن شیشه، استفاده از این ظروف در مایکروویو به منظور گرم کردن مجدد بلامانع می باشد.
ساخت ظروف شیشهای و نکات مهم مربوط به آن
۱- مواد اولیه
مهم ترین ماده مصرفی در تهیه شیشه مذاب و شکل دهی آن، سیلیس (Sio2) می باشد کـه ترکیـب عمـده شن و ماسه بحساب می آید که بطور طبیعی ۹۹ درصد آن را Sio2 تشکیل مـیدهـد. بـر حسـب مقـدار ناخالصـی موجود در شن و رنگ شیشه مورد نظر، تصفیه شن صورت میگیرد.
در صورتی که سیستم برگشـت شیشـه هـای مظروف به کارخانه وجود داشته باشد، دومین منبع مهم را همین شیشهها و یا خرده شیشه تشکیل میدهد. بخشـی از این خرده شیشه مربوط به ظروفی است که در حین کنترل کیفی مـردود شـده و مجـددا۲ بایـد ذوب شـوند. دو جزء بعدی و مهم، کربنات سدیم ( Na2Co3) و سنگ آهک (CaCo3) هستند. این دو ترکیـب در فرآینـد ذوب دمای ذوب را کاهش داده و تولید مقادیر زیادی گاز دی اکسیدکربن می نمایند که در حین حرارت دادن خـارج می گردد و همراه خود حبابهای هوا را خارج مینماید.
آلومینا (AL2O3) هم هرچند نه در حد وسیع در فرمـول وجود دارد. عمل اصلی آن بهبود و افزایش پایداری شیمیایی شیشه است. از مواد کمکی جهت افـزایش سـرعت
ذوب و خارج کردن گاز می توان استفاده نمود چراکه در غیر اینصورت درجه حرارت های بسیار بالا و زمانهـای طولانی مورد نیاز خواهد بود تا حباب ها کاملاخارج شوند.
از جمله این مواد مـیتـوان بـه ترکیبـات سـولفاته یـا سولفیدی اشاره نمود. در مورد رنگ، نکته حائز اهمیت آن است که تغییر رنگ از نوعی به نوع دیگر فرآیندی بسیار زمان بر می باشد و معمولاتا ۳۶ ساعت بطول میانجامد. امروزه برای غلبه بر این مشکل بجای افـزودن مـواد رنگی در کوره، آن ها را در پیشانی کوره (forehearth) که کوره را به دسـتگاه تولیـد ظـروف شیشـه ای متصـل می کند، اضافه می نمایند، هر چند با توجه به این که کوره اصلی، حاوی شیشه مذاب بـی رنـگ اسـت، بنـابراین نمی توان ضایعات شیشه رنگی که بدین ترتیب ساخته شده را به کوره بازگرداند.
انتقال مواد خام به درون کـوره به دو روش استفاده از مارپیچ ارشمیدسی و یا تیغه های عمودی متحـرک (ماننـد آنچـه در قسـمت جلـویی یـک بولدوزر دیده می شود)، انجام می گیرد. معمولامارپیچ، مواد را بصورت تپه ای (pile) وارد کوره مـیکنـد، حـال آنکه ورود مواد توسط تیغه الوار مانند (Log) خواهد بود. در هر صورت تجزیه ترکیبات کربناته و انجـام برخـی از واکنشهای شیمیایی در بدو ورود مواد اولیه و هنگامی که بصورت شناور بر روی توده مذاب قرار مـی گیرنـد، صورت خواهد گرفت.
۲- کوره و تجهیزات وابسته به آن
کوره معمولامستطیل شکل و تا ظرفیت ۴۰۰ تن ساخته مـیشـود و از یـک طـرف مـواد اولیـه وارد و از انتهای دیگر آنها شیشه مذاب خارج خواهد شد. درجه حرارت کوره تا ۱۵۰۰ درجه سانتیگراد میرسد، هرچند که در صورت استفاده از شیشه های بازیافتی ( recycled) و یا خرده شیشه (cullet) میتوان درجه حرارت را بین
۳۰۰ تا ۴۰۰ درجه سانتی گراد کاهش داد. دیواره کوره از قطعات بسیار بزرگ سیلیس ساخته شده اند که قابلیـت انعکاس حرارتی بالایی دارند. در ترکیب آنها و برای افزایش مقاومت، از آلومینا و اکسید زیرکونیوم نیز استفاده شده است. هر کوره از دو بخش تشکیل شده است که بوسیله یک قسمت شبیه به گلو شتر (depressed throat)
به یکدیگر متصل هستند. در قسمت اول مواد ورودی به صورت مذاب درآمده و ناخالصیها رسوب مـی نماینـد.
شیشه مذاب تحت تاثیر حرکت رانشی و از طریق شتر گلو از قسمت اول (پیش کوره) به قسـمت دوم یـا محفظـه کار (working chamber) وارد میشود. هدف عمـده از تعبیـه بخـش دوم در کـوره اولاتهیـه شیشـه مـذاب بـا خلوص بالا و ثان۲یا کاهش اندک درجه حرارت است بگونها ی که بتوان در مراحل بعدی شیشه مذاب را براحتـی وارد ماشین های ساخت شیشه نمود.سطح فوقانی کوره از قطعات سیلیسی خالص و بصورت مشبک (checkers)
و هلالی شکل ساخته می شود تا ضمن انعکاس حرارت به سطح توده مذاب شیشه، به خـروج گازهـا نیـز کمـک نماید. در کوره ها بخشی بـه نـام »بازیـاب حرارتـی(regenerator) « قـرار دارد کـه وظیفـه آن بازیافـت حـرارت خروجی از کوره و بازگرداندن آن به کوره می باشد. (شکل (۳ شیشه کـاملامـذاب همانگونـه کـه ذکـر شـد بـه پیشانی کوره (forehearth) وارد می شود که خود از دو قسمت خنک کننده پشتی و میانی و یک بخش مشروط کردن (conditioning) تشکیل شـده اسـت (شـکل .(۴ در قسـمت خنـک کننـده پشـتی، کـفگیـری و خـروج حباب ها نیز صورت می گیرد، زیرا که هنوز درجه حرارت توده خمیری شکل شیشه بالا می باشد.
با عبور توده از این قسمتها، درجه حرارت باز هم کاهش یافته تا در نهایت وارد بخش دیگری بنـام سیسـتم توزیـع ( feeding (distribution system گردد که شامل یک تا چهار بخش حلقوی شکل از جنس سرامیک است
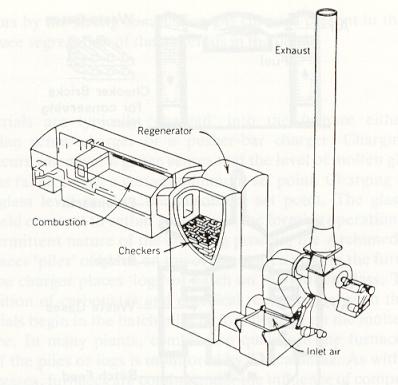
. این سیستم در انتهای پیشانی کوره قرار گرفته است. در همین قسمت است که کار تشکیل لقمـه (gob)
توسط پیستونهایی که بصورت عمودی رفت و برگشت انجام میدهند، صورت میگیرد (شکل .(۵
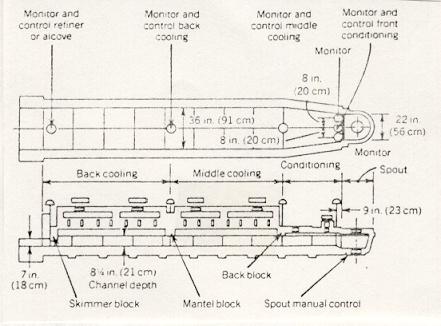
این لقمه ها ( که برحسب اندازه ظرف، دارای حجم و وزن متفاوتی میتوانند باشـند) توسـط قیچـی هـای افقی (shears) بریده شده وارد ناودان (scoop) می شوند. ناودان از طریق یک بخـش میـانی (through) و یـک منحرف کننده (deflector) (شکل (۶ به ماشینهای شکل دهنده لقمه ( Individual – seetion glass forming machine یا ( Is machine متصل میشود.
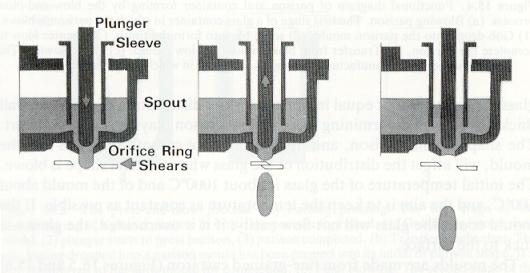
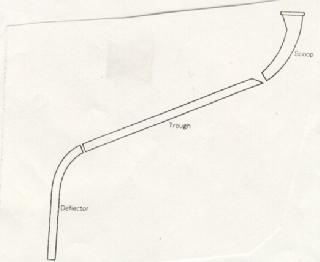
۳- شکل دهی
بخش شکل دهی بگونه ای طراحی شده است که بتواند لقمه های استوانه و خمیـری شـکل را بـه ظـروف میان تهی تبدیل نماید. ایـن فرآینـد از دو نـوع سیسـتم کـه هـر کـدام از دو مرحلـه تشـکیل شـده اسـت، جهـت شکل دهی استفاده می نماید. در مرحله اول تبدیل لقمه به یک ظرف اولیه به نام parison است که در مرحله بعـد این ظرف اولیه تبدیل به مظروف نهایی خواهد شد. دو سیستمی که جهت تولید ظروف شیشهای مصـرفی جهـت بسته بندی بکار میروند شامل روش دمیـدن و دمیـدن (blowing and blowing) اسـت کـه از آن جهـت تولیـد ظروف دهانه تنگ استفاده میشود و دیگر روش پرس کردن و دمیدن (pressing and blowing) میباشـد کـه از آن برای تولید ظروف دهانه گشاد بهره گرفته میشـود. در هـر دو حالـت مـاده اولیـه تکـه (lump) و یـا لقمـه
(gob) است که در مرحله اول توسط جریان هوا و یا یک سمبه (plunger) به شکل یک جسم میان تهـی کـه تـا حدودی شباهت به یک مظروف دارد در میآیند و سپس در مرحله بعد با استفاده از دمیدن به شکل نهایی تبدیل خواهد شد. در سیستم اول پس از آنکه قالب که شامل دو نیمه مجزا از هم میباشـد بسـته شـد لقمـه از بـالا وارد قالب می گردد. در این مرحله قالب به صورت واژگون قرار دارد، بگونه ایی که قسمت فوقانی مظروف در پـایین قرار گرفته است. پس از آنکه لقمه کاملادر انتهای قالب قرار گرفت، ضمن آنکه مرحله تشکیل finish صورت می گیرد، از بالا قالب بسته میشود. سپس هوا به درون لقمه دمیده شـده تـا شـکل اولیـه (parison) بدسـت آیـد.
آنگاه، قالب همراه با parison به صورت »سرپا« در آمده و مجددا۲ در آن دمیده میشود تـا شـکل نهـایی بدسـت آید. (شکل (۷ در انتها قالب باز شده ظرف خارج خواهـد شـد (شـکل .(۸ در سیسـتم دوم، در مرحلـه اول، کـار تبدیل لقمه به یک جسم میان تهی اولیه را یک سـمبه بعهـده دارد. ایـن ظـرف اولیـه و میـان تهـی پـس از آنکـه بصورت »سرپا« قرار گرفت توسط جریان هوا به شکل نهائی که عموما۲ یک ظرف دهانه گشـاد اسـت درخواهـد آمد. (شکل (۹ نکته مهم در هر دو سیستم تنظیم درجه حرارت است بگونه ایی که درجـه حـرارت لقمـه در بـدو ورود حدود ۱۰۰۰ درجه سانتی گراد و قالب ها حدود۵۰۰°C باشد درجه حـرارت هـای کمتـر باعـث مـیشـود تـا شیشه بخوبی قابلیت شکل پذیری نداشته باشد و درجه حرارت های بالاتر هم باعث مـی شـود تـا لقمـه بـه سـطوح بچسبد و یا بعد از شکل گیری تقارن خود را از دست بدهد. قالب ها از استیل ضد رنگ ساخته میشـود و کـاملا
سطح آنها صیقلی و صاف است ولی بهرحال، به مرور زمان دچار فرسایش شده و باید تعویض گردنـد. ایـن امـر خصوصا در مواردی مانند اندازه و قطر بدنه و finish و نیز دو محل اتصال قالبها به یکدیگر بسیار اهمیت دارد.
نکته جالبی که در ماشینهای ) IS که به آنها Independent machine هم گفته مـیشـود) وجـود دارد آن اسـت که میتوان بصورت همزمان چند نوع قالب را با اندازههای متفاوت بر روی آن نصب نمود البته با این فـرض کـه همه محصولات نیازمند لقمهایی با یک وزن مشخص باشند.
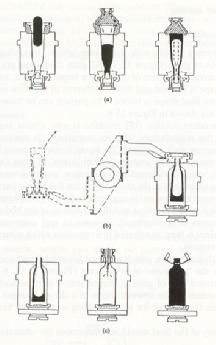
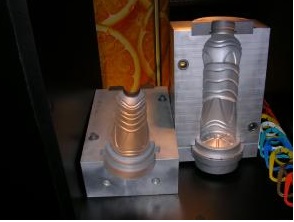
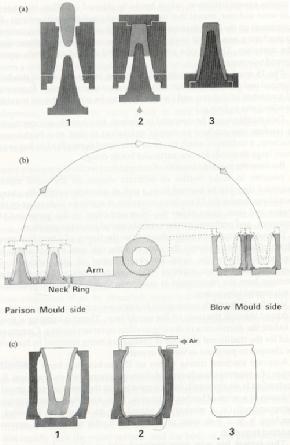
۴- استرس زدایی (Annealing)
آن کرده است میان مردم پیدا یژه ایی را درهنگامی که بطری یا ظرف شیشه ای از قالب خارج شد، درجه حرارت آن حدود۴۵۰ °C اسـت. اگـر بـه اجازه داده شود که بخودی خود سرد گردد، در این حالت تفـاوت سـرعت انقبـاض در بخـشهـای مختلـف شیشه باعث بوجود آمدن نوعی استرس در آن خواهد شد بگونه ایی که مظروف از ثبات کافی برخوردار نیسـت.
این امر از آن رو اتفاق میافتد که اصولا شیشه هادی حرارت خوبی نیست. با توجه به اینکه گرما در شیشـه بـاقی می ماند، سطح داخلی دیواره ظرف با سرعت کمتری نسبت به سطح خارجی خنک خواهد شد و حتی بدنه شیشه در میان دو سطح دیرتر خنک می گردد. بنابراین لازم است به نوعی سرعت خنک کردن و انقبـاض ناشـی از آن در شیشه تا سرحد امکان به شکل یکنواختی باشد. برای انجام این امر، ظروف ساخته شده به ماشین دیگری به نام ماشین استرس زداییAلر (Lehr)، که در واقع نوعی تونل طویل است منتقل میشوند. در این تونل درجه حـرارت به حدود ۶۰۰°C می رسد و سپس به تدریج عمل خنک کردن صورت می پذیرد (شکل .(۱۰ طـول تونـل حـدود ۴۰ متر است و درجه حرارت در انتهای آن به حدود ۳۰-۳۵ درجه سانتیگراد خواهد رسید.
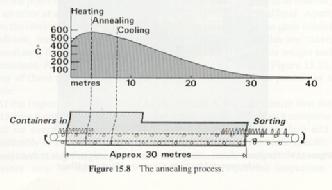
۵- آزمون ها
ظرف شیشه ای ساخته شده از چند نقطه نظر باید مورد بررسی قرار گیرد. ارتفاع، قطر بدنه ( و یـا ابعـادی که در ظروف غیر استوانه ایی مطرح هستند) و بالاخره finish از آن جملهانـد. بـرای کسـانی کـه ایـن ظـروف را جهت بسته بندی محصولات خود با استفاده از دستگاههای پرکن و درب بند، بکار میبرند، تغییرات شدید در هر یک از ابعاد گفته شده می تواند مشکلات فراوانی را بوجود آورد. حفره درون قالبها معمولابصورت متقـارن و یکدست دچار فرسایش نمی شود. این تفاوت در فرسایش سطح قالب که از آن تحت عنوان »بیضی شـکلشـدن« (ovality) یاد می گردد، باعث پدیدار شدن تفاوت در بین محورها خواهد شد.
خارج شدن از »حالـت عمـودی« (verticality) نیز که رابطه بین مرکز بطری در finish با مرکز همین بطری در پایه (base) بطری اسـت از دیگـر مواردی است که خصوصا۲ در بطریهای بلند دارای اهمیت بوده و در صورت عدم تقارن میتواند مشکلاتی را به هنگام قرار گرفتن بطری در زیر پرکن بوجود آورد. موضوع ظرفیت و گجایش ظروف هم از جنبـه هـای قـانونی دارای اهمیت است و باید کاملاکنترل شود و در این حالت از »آزمون انبوه(bulk test) « استفاده میشود. بـدین شکل که حجم داخلی تعدادی ظرف اندازهگیری شده و سپس میانگین آنها با استاندارد مقایسه میشود.
۷- استرس ها
ظروف شیشهای ساخته شده در نهایت به کارخانه های بسته بندی مواد غذایی وارد مـی شـوند تـا از آنهـا جهت بسته بندی استفاده شود. در این کارخانه ها نیز ظروف با یکسری استرس ها یا فشارها مواجـه مـی باشـند کـه مهمترین آنها عبارتند از:
الف: فشار داخلی (مثبت یا منفی)
در محصولاتی که تحت فشار یا تحت خلا بسته بنـدی آنهـا در ظـروف شیشـه ای انجـام مـیگیـرد دیـده میشود. در یک بطری فشار داخلی عمدتا۲ باعث بروز استرسهای محیطی (محیط ظرف) و طولی خواهد شد. در بخش استوانه ای، استرس محیطی (S) بسـتگی بـه قطـر بطـری (d)، ضـخامت شیشـه (t) و فشـار وارده (p) دارد و میتوان آن را به شکل ذیل محاسبه نمود.
S =pd / 2t
فشار طولی معمولانصف فشار محیطی خواهد بود. در بخش های غیر استوانه ای معمولابدلیل تفاوت در ضخامت و تغییرات شدید انحناها، از معادلههای پیچیدهتری باید استفاده نمود.
ب: استرسهای ناشی از بار عمودی
بواسطه روی هم چیدن ظروف و یا به هنگام درب بندی (طشتک زنی) ایجاد میشود. ایـن نیروهـا بیشـتر به نواحی شانه و پاشنه ظروف وارد می شود. معمولااین نوع استرس را می توان با طراحـی مناسـب کـم نمـود. از جمله می توان تفاوت مابین قطر بدنه و قطر گردن را کاهش داد که در واقع افزایش شـعاع شـانه ظـرف را در بـر خواهد داشت. همچنین می توان تفاوت قطر بدنه و قطر سطح اتکا ظرف (bearing surfac) را نیز کم نمود.
ج: استرسهای تماسی و ضربهای
این نوع استرس ها هنگامی ایجاد می شوند که ظروف به یکدیگر یا به شـئی دیگـری برخـورد و اصـابت نمایند و بیشتر به هنگام پرکنی، حمل و نقل و مصرف رخ میدهد. برای رفع آن استفاده از پوشش ثانویه میتواند مفید باشد.
د: استرس ناشی از شوکهای حرارتی
که به هنگام تغییرات سریع حرارتی مثلادر پاستوریزه شدن و یا پرکردن محصول به صـورت گرمـا گرم (hot filling) دیده میشود. این نوع استرسها را میتوان با محدود نمودن تفاوت درجـه حـرارت در قسـمتهای سرد و گرم، کاهش ضخامت شیشه و اجتناب از ایجاد زوایای تند در سـاختار شیشـه خصوصـا۲ در قسـمت پاشـنه (thin spot) از بین برد و یا کاهش داد. (شکل .(۱۱
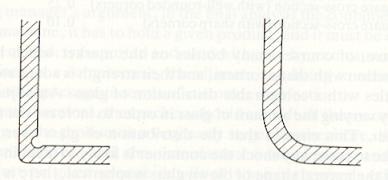
۷- واژه شناسی ظروف شیشهای
ظروف ساخته شده از قسمت های مختلفی تشکیل شده اند که آشـنایی بـا آنهـا مـیتوانـد در بخـش هـای طراحی های جدید و یا مقابله با استرسها، مفید واقع شـود. شـکل ۱۲، ایـن قسـمت هـا را در بطـری و جـار نشـان میدهد.
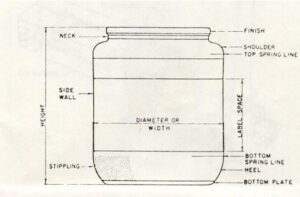
۸- تیمارهای سطحی
از این تیمارها باعث بهبود خواص شیشه خصوصا۲ از نظر ظاهر و افزایش مقاومت به ضربه میشود.
الف: تیمار گرم
معمولاپس از تولید، شیشه دارای ترکهای ریز (microcracks) در سطح خود است که میتواند باعث آسیبپذیری شیشه شود. با اسپری نمودن محلولی از یک فلز همراه با مواد آلی بر روی سطح ظروف شیشهائی به هنگامی که سطح آنها هنوز داغ است، می توان از پیدایش این ترکها جلـوگیری نمـود. معمـولااز ذرات بسـیار ریز قلع و یا ترکیبی چون تیتانیوم تتراکلراید استفاده میشود.
ب: تیمار سرد
در این حالت، امولسیونی از انواع مومها و یا روغن ها بصورت سرد بر روی شیشه پاشـیده مـیشـود. ایـن عمل را میتوان در قسمتهای انتهایی ماشین لر انجام داد.
ج: پوشش با ترکیبات پلیمری
ابتدا PVC و بعد پلی اتیلن بویژه در مورد شیشه های نوشابه گازدار بکار گرفته شد، اما به دلیل مشـکلاتی که وجود داشته اکنون توجه به استفاده از رزین های یونومری معطوف شده است. علاوه بر این موارد اسـتفاده از
«sleeves» (پوشش آستین مانند)که گرداگرد بسته شیشهای قرار میگیرد، نیز معمول می باشد (شکل .(۱۳
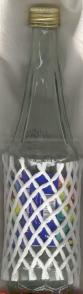
۹- کاهش وزن شیشه
تلاش زیادی بعمل آمده است تا از وزن ظروف شیشه ای کاسته شود. این کاهش علاوه بر مصرف کمتر مواد اولیه، باعث صرفه جویی در هزینههای حمل و نقل نیـز خواهـد شـد. البتـه توجـه بـه طراحـی و نحـوه انتقـال حرارت می تواند راهگشا باشد. کاهش ضخامت هرچند آسیب پذیری را افزایش می دهد اما در عین حال با توجه به اینکه در نحوه تعامل شیشه و حرارت اثر مثبتی دارد، می تواند باعث افزایش ثبات آن گـردد. انجـام تیمارهـای شیمیایی مانند آنچه در ژاپن تحت عنوان (chemical strengthening treatment) CST صـورت مـیگیـرد نیـز مورد توجه می باشد. همچنین توجه به نیروی کشش شیشه که در عمل بین ۷۰۰ تا ۱۴۰۰ کیلـوگرم بـر سـانتیمتـر مربع است و بنابراین انتخاب وسایل درببندی در محدوده فوق، همگام با کاهش ضخامت توصیه میگردد.
۱۰- درب ظروف شیشه ایی
همانگونه که ذکر شد، ظروف شیشه ای در دو نوع دهانه گشاد یـا جـار و دهانـه تنـگ یـا بطـری سـاخته می شوند. در هر دو مورد استفاده از درب که محکم بر روی شیشه قرار گیرد ضروری میباشد. این دربها بطور کلی از جنس فولاد قلع اندود یا آلومینیوم ساخته شده کـه در قسـمت داخلـی دارای پوششـی کـه معمـولانـوعی ترکیب پلاستیکی مثلاPVC 2 و یا سایر مواد پلی مری است، میباشد.
بـرای آنکـه درب بنـدی بـه شـکل محکمـی انجام شود از روشهایی مانند فشار دادن، پیچیدن، چرخاندن و مانند آنها استفاده می گردد. درب ها ممکـن اسـت به صورت تاجی شکل، لبهدار و چرخشی دیده شوند.
الف: درب ظروف دهانه گشاد:
دو نوع دربguard–seal و tamper–seal از انواعی هستند که به شکل گسترده ایی از آنها در مـواردی که محصول تحت خلاء عرضه می شود، استفاده میشود. در این نوع درب بندی نوعی قسمت یقه مانند، لبـه هـای درب و بخشی از شانه ظرف را میپوشاند. (شکل.(۱۴ از دربهای لبهدار (lug cap) نیز برای بسته بندی میوهها و سبزیها، ترشیها، مرباها، ژلهها، آبمیوهها و مانند آنها استفاده میشود.
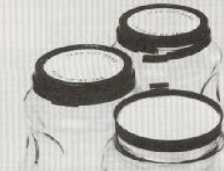
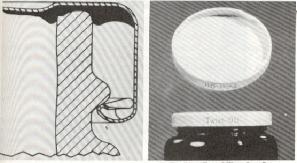
به این نوع در ها twist-off هم گفته می شود. شکل ۱۵ این نوع در را نشان میدهد. نوع دیگری از همین در press–on twist off نام دارد که بدون واشر بوده و با فشار لبـه در بـر روی finish ظـرف شیشـه ائـی درگیـر می شود (شکل.(۱۶ در لیوانی کـه مخصـوص ظـروف لیـوانی شـکل اسـت و در آن از تعـداد بیشـتری لبـه (lug) برخوردار است، نیز از همین دسته محسوب میشود (شکل .(.۱۷
ب: در ظروف دهانه تنگ این در ها به دو دسته قابل بسته شدن مجدد و غیرقابل بسته شدن مجدد تقسیم مـیگردنـد. در حالـت دوم
در اصطلاحاcrown2 یا تاج نامیده شده و معمولااز جنس فولاد قلع اندود است. ایـن در هـا دارای لبـه کنگـرهدار
(fluted–skirt) بــوده کــه بعــد از قــرار گــرفتن بــر روی دهانــه بطــری، بــدور finish جمــع (crimp) می شـوند
(شکل.(۱۸
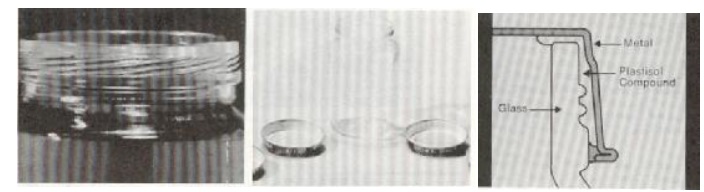
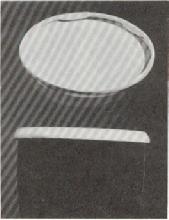
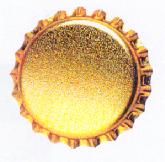
امروزه نوعی از آن به نام easy–open twist–off crown به بازار عرضه شـده کـه بـر روی آنهـا نـوعی شیار (thread) دیده می شود بگونه ای که به آنها امکان باز و بسته شدن مجدد را می دهـد. درب هـای بطـری کـه قابل بسته شدن مجدد هستند عموما۲ از جنس آلومینیوم بوده و به صورت roll–on بسته میشوند. مهمتـرین انـواع آنها با قطر ۲۶ و ۲۸ میلی متر است ولی انواعی با قطر ۴۰ میلیمتر نیز ساخته مـیشـود. ایـن نـوع درهـا فاقـد شـیار متناسب با finish هستند و پس از آنکه بر روی دهانه بطری قرار گرفتنـد، بـر اثـر فشـار در بنـد شـیار متناسـب بـا finish بر روی آنها ایجاد میشود (شکل.(۱۹
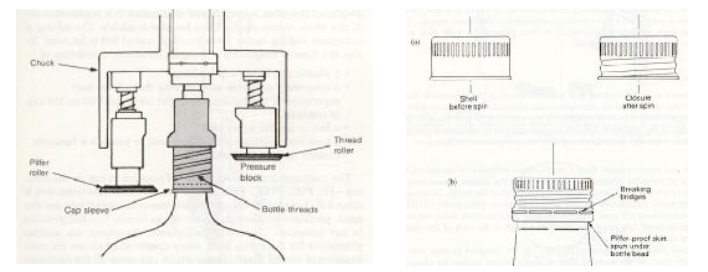
این نوع درها دارای نواری نازک در بخش پایینی هستند که با پلهایی به درب اتصال دارند و نقش ضد ناخنک زدن (tamperproof or pilfer–proof) را بعهده دارند. تمامی درهای ظروف دهانه تنگ نیز از داخل با لایه ای از مواد پلی مری مانند PVC پوشیده شده اند. به این لایه ها liner یا آستری گفتـه مـیشـود. آخـرین نکتـه درباره در ظروف آن است که این وسیله بخشی از بسته است و باید از جمیع جهات با آن هماهنگ باشد و تحت هیچ شرایطی با محتویات واکنش ندهد.